How A Formula 1 Internal Combustion Engine Works
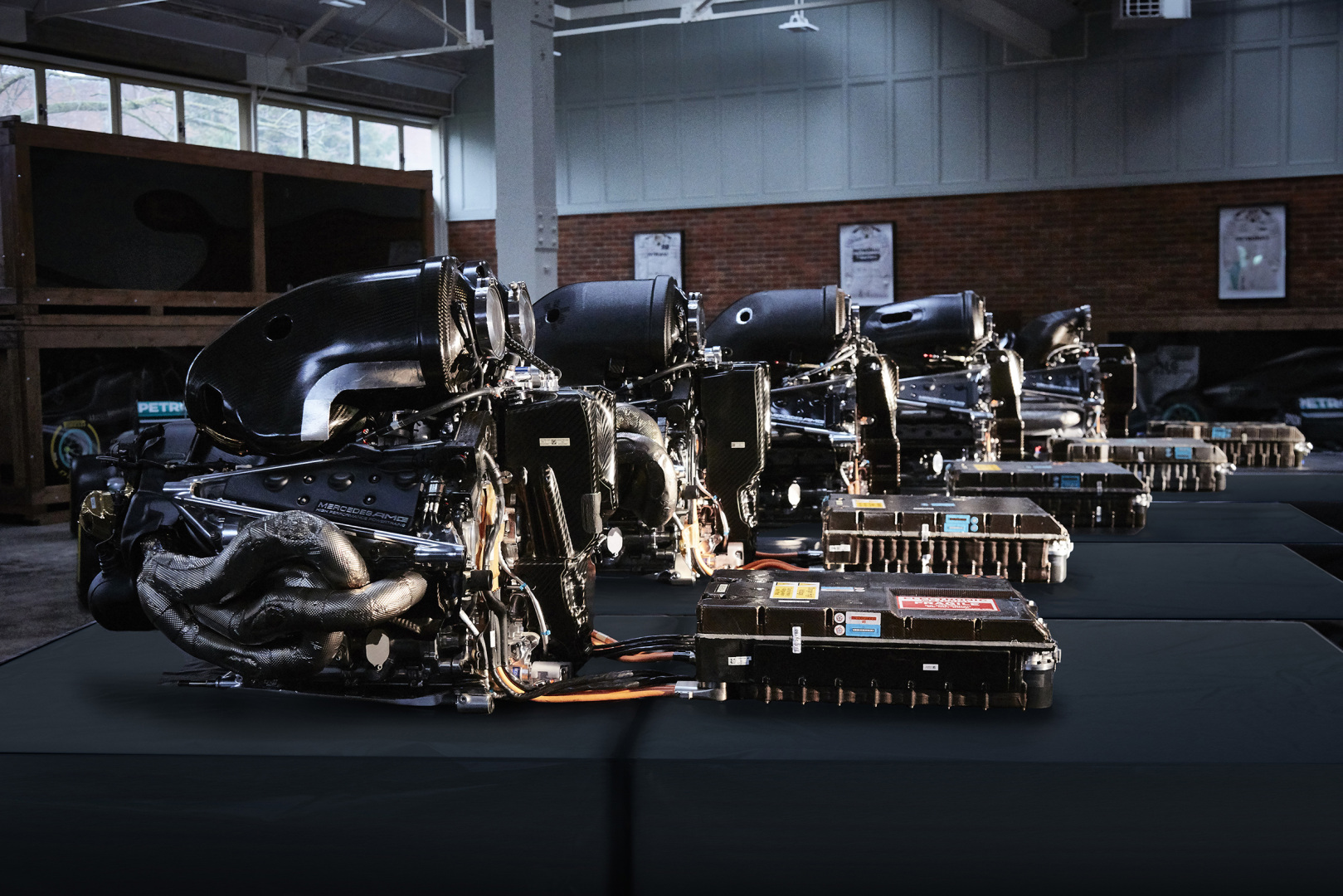
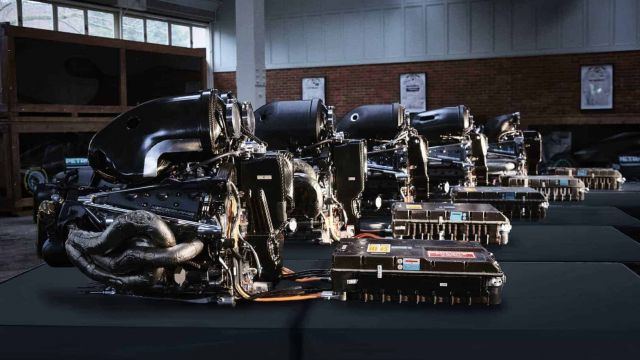
The Formula 1 internal combustion engine (ICE) is a marvel of engineering, designed for high performance and efficiency within the confines of racing regulation. Each engine is a 1.6-liter V6, augmented by turbocharging to significantly increase its power output. Fitted within a hybrid power unit framework, these engines are connected to advanced energy recovery systems (ERS) which harness waste energy to boost power further or save it for strategic use during a race. The result is an engine that can produce approximately 1,000 brake horsepower (bhp).
The efficiency of these engines is also critically managed through tight fuel flow regulations, which limit the amount of fuel that can be used per hour, thus ensuring the teams push the boundaries of fuel efficiency. Alongside this, sophisticated cooling systems maintain the temperature, necessary because these engines and their accompanying ERS components operate under extremely high thermal stress. The technology evolves continuously with the evolving regulations, maintaining Formula 1’s status at the forefront of automotive engineering achievements.
Key Takeaways
- Integration of Advanced Hybrid Technologies: Formula 1 engines transcend traditional boundaries by integrating a 1.6-liter V6 turbocharged engine with sophisticated Energy Recovery Systems (ERS), showcasing a blend of raw power and advanced technology to achieve around 1,000 brake horsepower. This highlights Formula 1’s pioneering role in pushing the envelope of automotive engineering.
- Strategic Adaptation to Regulatory Constraints: The evolution and efficiency of Formula 1 engines are significantly influenced by stringent fuel flow regulations and the need for effective thermal management. These constraints drive teams to innovate continuously, ensuring engines not only comply with regulations but also optimize performance and fuel efficiency within these bounds.
- Synergy Between Power and Efficiency: The meticulous design of Formula 1 engines and their auxiliary systems exemplifies a perfect synergy between achieving maximum power output and maintaining high efficiency. This delicate balance is maintained through the strategic use of fuel, precise control of engine temperature, and the repurposing of waste energy, illustrating the sport’s commitment to both performance and sustainability.
Overview of Formula 1 Power Units
This section provides a concise outlook on the technological masterpiece that is the Formula 1 power unit, encompassing its definition, componentry, and critical role within a Formula 1 car.
Definition and Evolution of Power Units
The term power unit in Formula One refers to the sophisticated combination of an internal combustion engine (ICE) and auxiliary systems like the energy recovery system (ERS). Over time, these power units have evolved from simple engines to highly complex systems. The modern Formula 1 power unit is a 1.6-liter V6 turbocharged engine equipped with advanced technologies to optimize performance and efficiency.
Components of a Power Unit
A Formula 1 power unit includes several key components that work in concert:
- Internal Combustion Engine (ICE): The core of the unit, a 1.6-liter V6 engine, capable of running at 15,000rpm.
- Turbocharger: Boosts engine power by using exhaust gases.
- Energy Recovery System (ERS): Comprises two motor generator units—the MGU-H (harvests energy from the turbocharger) and MGU-K (recovers kinetic energy during braking).
- Control Electronics: Manages the power unit’s various elements and their interaction.
These systems are integrated to maximize the power output, which can exceed 1000 bhp.
Role in a Formula 1 Car
The power unit is at the core of a Formula One car’s performance. It does not simply propel the car with formidable speed; it also contributes to the car’s braking and energy management. The harmonized operation of the electric motor and ICE enhances fuel efficiency and ensures compliance with Formula 1 regulations, which mandate the use of hybrid engines with a fuel flow limit.
Internal Combustion Engine (ICE) Mechanics
The internal combustion engine (ICE) within a Formula 1 car is a pinnacle of automotive engineering, transforming fuel into the speed and power that propels the world’s fastest racing cars. The mechanics of this complex component are crucial for the vehicle’s performance on the track.
Understanding the Combustion Process
The combustion process is initiated in the combustion chamber where a precise mixture of air and fuel is ignited. A Formula 1 ICE typically uses a turbocharged V6 engine, with a 1.6-liter displacement, where the following sequence takes place:
- Intake stroke: The air intake valve opens, allowing air and a regulated quantity of fuel to enter the combustion chamber.
- Compression stroke: The intake valve closes, and the piston compresses the mix, increasing pressure and temperature.
- Power stroke: A high-voltage spark from the spark plug ignites the mixture, creating a controlled explosion that pushes the piston down, generating mechanical power.
- Exhaust stroke: The exhaust valve opens to allow burnt gases to escape, making room for the next cycle.
Fuel and Air Mix Dynamics
The dynamics of the air-fuel mixture are crucial for maximum efficiency and power output. The engine’s electronic control unit (ECU) moderates the fuel delivery and air intake to achieve the stoichiometric balance — the ideal ratio for combustion. Factors such as air temperature, barometric pressure, and engine load affect this mixture. In F1, turbochargers compress incoming air to increase its density, thus enhancing combustion and power.
Exhaust Gases and Energy
Post-combustion, exhaust gases hold residual energy as they exit the engine at high velocity. In an F1 ICE system, this energy is not wasted. The gases spin a turbine connected to the turbocharger, recycling energy to compress incoming air. Additionally, an advanced component called the MGU-H (Motor Generator Unit-Heat) captures heat energy from the exhaust to improve overall efficiency and boost electrical energy available to the power unit. This intricate convergence of mechanical and thermal processes delineates the sophistication of the power units used on the race track.
Turbocharging and Boost Pressure
Turbocharging significantly elevates the power output of a Formula 1 internal combustion engine by forcing more air into the combustion chamber, which in turn allows for more fuel to be burned, generating more power. The manipulation of boost pressure and the control of turbo lag are critical for maximizing engine performance and efficiency.
How Turbocharging Works
A turbocharger is a forced induction device that increases an engine’s efficiency and power output by forcing extra air into the combustion chamber. This is achieved by a turbocharger compressing the air that flows into the engine. The core components of the turbocharger include a turbine and a compressor connected by a common shaft. The exhaust gas from the engine spins the turbine, which then spins the compressor, drawing in and compressing air. The increased air density enhances the engine’s ability to burn fuel, resulting in increased power and torque.
Management of Boost Pressure
- Control Systems: Formula 1 cars employ sophisticated control systems to manage the boost pressure. These systems adjust the turbocharger’s performance to match the driver’s demand for power.
- Wastegate: A wastegate is utilized to prevent overboosting by redirecting some exhaust flow away from the turbine, controlling the maximum boost pressure produced by the turbocharger.
- Regulations: The regulations imposed by the Fédération Internationale de l’Automobile (FIA) also influence how teams manage boost pressure, ensuring a level playing field and safety.
Effects of Turbo Lag
Turbo lag refers to the delay between the driver’s throttle input and the turbocharger’s delivery of increased boost pressure. It’s perceptible as a pause before the acceleration kicks in after the driver steps on the throttle. This occurs because the turbocharger’s turbine needs to speed up (spool) adequately to produce the required boost pressure, which doesn’t happen instantaneously.
- Spooling: Once spooled, the turbo’s spinning can reach speeds up to 150,000 RPM or higher, illustrating the stresses it undergoes.
- Minimization Strategies: F1 engineers employ various strategies to reduce turbo lag, such as the Motor Generator Unit – Heat (MGU-H) to utilize exhaust gases efficiently, and designing responsive turbocharger systems that can quickly adjust to changes in throttle.
Energy Recovery Systems (ERS)
Formula 1’s Energy Recovery Systems (ERS) are crucial for enhancing efficiency and power. These systems capture energy that would otherwise be wasted and repurpose it, providing a significant boost to the car’s performance.
Harnessing Kinetic Energy – Motor Generator Unit-K
MGU-K (Motor Generator Unit – Kinetic) is responsible for recovering kinetic energy during braking. When the car decelerates, the MGU-K transforms this kinetic energy into electrical energy, which is then stored for later use. This stored energy can be deployed to provide additional power to the crankshaft during acceleration, effectively functioning as an electric motor to aid the internal combustion engine.
- Energy Recovered: Kinetic energy during deceleration
- Function: Transforms into electrical energy
- Use: Additional power when accelerating
Heat Energy Conversion – Motor Generator Unit-H
MGU-H (Motor Generator Unit – Heat) works to convert heat energy from the engine’s exhaust gases. The energy harnessed by the MGU-H is used to either power the MGU-K or to spin the turbocharger to reduce turbo lag, thereby improving engine responsiveness. The process involves capturing the heat produced during combustion, which would typically be lost, and transforming it into electrical energy.
- Energy Recovered: Heat energy from exhaust gases
- Function: Powers MGU-K or assists the turbocharger
- Use: Reduced turbo lag, enhanced responsiveness
Fuel Flow and Regulation
Controlling fuel flow is critical for Formula 1 engines to meet performance and regulatory requirements set by the FIA.
Fuel Flow Metering
The fuel flow meter is an essential component in a Formula 1 car that precisely measures the amount of fuel injected into the combustion chamber. Regulations specify that teams must use a homologated fuel flow meter provided by an FIA-approved manufacturer. This device ensures that the fuel delivery complies with the preset limits and that all teams have a level playing field.
Formula 1 Fuel Flow Limits
The FIA introduced stringent fuel flow limits to regulate the maximum amount of fuel that can be used during a race and maintain a balance between performance, safety, and sustainability. The fuel flow limit is typically set at a maximum rate of 100 kilograms per hour. Compliance with these fuel flow rates is monitored in real-time by the FIA to guarantee that no team exceeds the permitted limits during the race.
Hybrid Technology Integration
Formula 1 has significantly evolved with the integration of hybrid technology, blending internal combustion engines (ICE) with sophisticated electric systems to enhance performance and efficiency.
Combining ICE and Electric Systems
The hybrid systems in Formula 1 consist of an ICE and an electric power unit. The ICE traditionally utilizes a turbocharged V6 engine to provide the primary source of propulsion. In parallel, the electric power unit capitalizes on additional energy sources. This electric power is harvested during braking or exhaust flow and then stored for subsequent use.
Energy Storage and Deployment
F1 hybrid systems store electric energy in an energy store, typically using advanced li-ion cell technology. This allows stored energy to be rapidly deployed, giving drivers an extra boost of power on-demand. This boost is carefully managed to provide strategic advantages during overtaking or defending positions on the track. The deployment is regulated to ensure consistency and fairness in the competition.
Electrical Energy Utilization
In Formula 1, electrical energy plays a critical role in boosting the power unit’s performance through sophisticated energy recovery and repurposing mechanisms.
Role of Energy Store
The Energy Store (ES), a component of the F1 power unit, is responsible for storing and supplying electrical energy. The ES can be likened to a high-tech battery system that efficiently manages the energy harvested during different phases of the race. This unit is not only crucial for energy storage but also for maintaining the balance and delivery of power when the car transitions between braking and accelerating.
- Storage Capacity: An ES has limited capacity, making its management during the race essential.
- Durability: Each driver is allocated a limited number of ES units for a season, underscoring the importance of reliability.
Electric Motor and Energy Repurposing
The Motor Generator Unit – Kinetic (MGU-K) serves as the pivotal electric motor that assists in energy repurposing. When a Formula 1 car brakes, the MGU-K acts as a generator by converting the kinetic energy usually lost as heat into electrical energy. This electrical power is then either directly supplied to the drivetrain for an instant power boost or stored in the ES for later use.
- Direct Power Contribution: Electric power from the MGU-K provides an immediate additional boost, increasing the car’s speed on demand.
- Strategic Management: Teams meticulously manage the repurposing of energy to gain a tactical advantage on the track.
Cooling Systems and Thermal Management
Formula 1 engines, with their high power output, generate substantial heat, necessitating advanced cooling systems for optimal performance and reliability. Effective thermal management is vital to maintain engine efficiency and prevent damage through overheating.
Importance of Engine Cooling
The engine is the heart of a Formula 1 car, and managing the heat it generates is critical for several reasons. Firstly, overheating can lead to engine failure, which can end a race prematurely. Secondly, high temperatures can reduce the efficiency of the engine and its power output. Constant exposure to heat can degrade various components, leading to a decline in performance over time.
- Prevents Engine Failure
- Ensures the integrity and longevity of engine components
- Reduces the risk of sudden breakdowns during races
- Maintains Efficiency
- Preserves optimal engine performance
- Enables sustained power delivery from the internal combustion engine (ICE)
Cooling Solutions for High Performance
F1 teams employ various cooling solutions to manage the thermal dynamics of their engines. These solutions are critical in striking a balance between performance and reliability. Given that a modern F1 ICE reaches high temperatures, almost half as hot as the surface of the sun in the combustion chamber, adequate cooling is vital.
- Air Cooling
- Channels airflow through critical areas
- Utilizes aerodynamically designed inlets and outlets
- Liquid Cooling
- Employs coolants that circulate through the engine block and heads
- Transfers heat to the radiators, where it is dispersed
- Exhaust Systems
- Optimizes the flow of hot exhaust gases away from the engine
- Includes advanced materials to withstand extreme temperatures
The hybrid systems, combining the ICE with electrical components, add complexity to the F1 car cooling demands. Teams fine-tune the balance: too much cooling adds weight and increases aerodynamic drag, while too little risks overheating and part failure.
Monitoring and Control
In Formula 1, the internal combustion engine (ICE) performance is heavily dependent on precise monitoring and controlled management systems. These systems work in unison to maintain performance, reliability and conform to regulations, particularly concerning fuel flow rates.
Role of Control Electronics
Control electronics play a pivotal role in managing the engine and other components of the power unit. These specialized systems control the fuel injection, ignition timing, and turbocharger operation for optimal performance. Engine manufacturers implement sophisticated software within these electronics to regulate processes and adapt to the demands of the race.
- Fuel Flow: Governed by control electronics to adhere to FIA’s limitations.
- Turbocharger: Adjustments made in real-time to manage air intake and efficiency.
Data Acquisition and Performance Tuning
Data acquisition systems are essential for collecting detailed information on the engine’s operation. Teams analyze this data to make informed decisions on performance tuning for different track conditions.
- Engine Mapping: Adjusts power delivery and fuel consumption.
- Performance Tuning:
- Power Units: Tuned for maximum output while maintaining reliability.
- Fuel Consumption: Strategically managed for race longevity and power.
Evolution of Engine Regulations
The regulations governing the power units in Formula 1 have seen significant transformations, directly influencing the designs and capabilities of Formula 1 race cars over the decades.
Historical Changes in Engine Rules
Historically, Formula 1 has cycled through various engine formats, each dictated by changing rules from the Federation Internationale de l’Automobile (FIA). In the early days, there was considerable freedom, but in the quest for safety and parity, regulations tightened. In order to balance performance and maintain competition, engine rules have consistently evolved.
- 1950s to 1960s: The era started with 4.5-liter naturally aspirated engines which later were constrained to 1.5 liters.
- 1970s to 1980s: The introduction of turbocharged engines saw power outputs soar, leading to a 1.5-liter limit for turbos in 1977.
- 1990s: Rules mandated 3.5-liter naturally aspirated and then 3.0-liter engines by the mid-90s.
- 2000s: Engine sizes were further reduced to 2.4 liters V8, limiting the number of revs and engine changes over a season to ensure durability.
- 2014 to present: The current regulations require 1.6-liter V6 turbocharged engines equipped with Energy Recovery Systems (ERS), marking the hybrid era.
Impact of Regulations on Engine Design
Engine manufacturers have continuously adjusted their designs to adhere to the FIA’s regulations, which aim to ensure both competitiveness and safety within Formula 1. Regulatory changes have had a substantial impact on engine design, with manufacturers such as Ferrari, Mercedes, Renault, and Honda reconfiguring their power units for optimal performance within set parameters.
- Fuel Efficiency: New rules often promote greater fuel efficiency, like the current hybrid engines with fuel flow limits.
- Environmental Concerns: Regulations steer designs towards reduced environmental impacts, encouraging hybrid technologies and lower emissions.
- Performance Restrictions: Measures such as rev limits and fuel flow restrictions limit peak power outputs, requiring clever engineering solutions.
- Reliability Mandates: With penalties for excessive engine part replacements, manufacturers focus on the longevity of each component, alongside their performance.
F1 Engines -FAQs
What elements make up a Formula One Power Unit?
The FIA distinguishes between six elements in a modern F1 Power Unit (PU). At the very heart of the PU sits the Internal Combustion Engine (ICE). It’s a structural member of the car, connecting the chassis to the gearbox.
The current F1 engines are six-cylinder engines, constructed in a V-configuration at 90 degrees, with a 1.6-litre displacement.
The second element is the turbocharger (TC), which increases the density of the air that is consumed by the engine, thus giving the engine more power.
A modern F1 engine is a hybrid engine, with two electric machines recovering and delivering energy. There’s the Motor Generator Unit-Kinetic (MGU-K), which harnesses kinetic energy when the car is braking, and the Motor Generator Unit-Heat (MGU-H), which is connected to the turbocharger and harnesses excess energy from the exhaust.
Both motor generator units convert their respective energy sources into electrical energy which can then be used to propel the car. The electric energy is stored in the fifth element of the Power Unit – a big battery pack known as the Energy Store (ES).
This intricate system of different components is controlled by the sixth and final element, the Control Electronics (CE).
Drivers are permitted three ICE, MGU-H and TC and two ES, CE and MGU-K during the course of a season, but any combination of parts can be fitted to the car. If a driver exceeds this limit, they are given a grid penalty.
How does the combustion process work in a Formula 1 Internal Combustion Engine?
At the heart of the ICE is the combustion process where fuel and air are mixed and ignited to liberate energy. This process works in the same way it does on your road car; however, the systems are a bit more intricate.
Looking at it in more detail, the combustion air is fed to the engine through an air duct that sits behind the roll hoop. The air pressure is increased by a compressor which is part of the turbocharger.
This process also increases the air temperature, so the air needs to be cooled again in a charge cooler before it’s fed into the plenums at the top of the engine.
From there, it passes down the six inlet ports and past two inlet valves into the cylinders. That’s where the fuel comes into effect.
F1 engines are direct injection, like most modern road cars, so the fuel is injected directly into the combustion chamber.
The fuel is injected at a maximum of 500 bar, which is limited by the regulations. While that is more than you would find on a direct-injection petrol engine in a road car, which usually sees pressures of up to 350 bar, it is actually quite a bit less than you might find in a modern diesel, where fuel pressures can reach up to 2,500 bar.
The air and fuel mixture is compressed by the piston before a spark plug ignites it. The force of the combustion pushes down the piston, which is connected to the crankshaft through a connecting rod and is, therefore, able to drive the crankshaft.
When the piston comes back up, the exhaust valves open to release the exhaust gases from the engine, so that the whole process can start all over again – up to a maximum of 15,000 times every minute (or up to 250 times a second).
The exhaust gases are used to drive the turbine wheel of the turbocharger which in turn drives the compressor. What’s left then exits through the tailpipe at the rear of the car, with a wastegate system being used to control the pressure during this phase.
What other systems are part of the F1 Internal Combustion Engine?
Very intricate and complex oil and water systems are also featured in the engine, weaving between the different elements.
These keep the engine running smoothly and regulate temperature, which is incredibly important when you consider that the gas temperatures in the combustion chamber can reach up to 2,600°C.
The water system’s main job is to manage the temperatures of the many different elements and materials that make up the F1 Power Unit. From the crankcase to the top of the cylinder head, it’s all about making sure the engine doesn’t overheat.
A great deal of engineering goes into that, from managing the flow of water, to the pump efficiency.
What role does Formula 1 fuel play in the hunt for performance?
Formula 1 fuel is at the very heart of the combustion process and has a significant influence on the performance of the engine. The regulations state that the fuel needs to be unleaded, so it’s like the kind of fuel you would use in a road car.
Does that mean you could potentially run an F1 Power Unit with regular road car petrol from your local filling station? You could – but it would require some changes to the calibration, for example to the ignition.
You would also experience a very noticeable drop in performance. Why? Because the PETRONAS Primax fuel that the team uses has been developed over the last eight years and is minutely calibrated to work perfectly with the Mercedes Power Unit.
A group of PETRONAS engineers is constantly working on the chemical composition of the fuel to make sure its characteristics match those required by the engine. This development work is done in close cooperation with the thermodynamic engineers at HPP.
How long does it take to build a Formula 1 Power Unit and what is the process?
Power Units are complex machines and the more powerful they’ve become, the more complex they’ve grown. Back in 2014, it took a team of two people about two weeks to build a Power Unit.
Fast forward to 2019 and the same task would take about three weeks with the same number of people. Therefore, the team at Brixworth had to try and condense that time so that it wouldn’t lose precious development time to the build process, and to do so, they added more people to the build process. So, two weeks has been maintained but with an additional person involved.
Are Formula 1 engines hybrid?
In 2014, hybrid components were introduced, resulting in a change in terminology. Rather than just ‘engines’, modern F1 cars are all fitted with a whole ‘power unit’ system. An Internal Combustion Engine (ICE) forms the heart of these power units. This is the V6 engine with a 1.6-litre displacement.
A turbocharger has been added to this ICE. By increasing the density of the air the engine breathes in, this device increases its power. The exhaust-driven turbine also helps generate additional power from residual engine heat.
On top of the ICE and Turbocharger, there is a full Energy Recovery System (ERS), which captures the energy produced by the car on track, stores it, and can then re-use it to provide more power. The redeployed power is equal to 160 horsepower, which can be used for up to 33 seconds of a racing lap.
Two of the ERS’s most crucial components are the MGU-H and MGU-K. The exhaust gases are used to power the MGU-H (Motor Generator Unit – Heat). Rather than letting heat escape through the exhaust, the MGU-H harnesses it and converts it into electricity. By capturing the escaping heat, the MGU-H generates electricity and returns it to the Energy Store as the engine and turbo increase speed.
An electric generator and motor together make up MGU-K (Motor Generator Unit – Kinetic). It provides power under acceleration when connected to the ICE. During braking, it also generates energy. Normally, the heat that would escape the brakes is captured and used to generate electricity that is stored in the Energy Store.
Simply put, the Energy Store (ES) is the car’s battery. Energy generated by the ERS is stored here until it is needed for deployment. During one lap, it can store and redeploy up to 4 megajoules of energy.
The Control Electronics (CE) integrates all other components of the ERS together. The code ensures that all the systems communicate with each other and work properly.
For a Formula 1 car, each of these components is crucial. If a single part of the Energy Recovery System fails, a car may be able to drive, but it will result in mechanical issues, a loss of speed and power, and increased fuel consumption. The car is unlikely to finish a race if one of these parts fails.
What engines are used in Formula 1?
A Formula One engine is currently a 1.6 litre four-stroke double-overhead camshaft (DOHC) reciprocating four-stroke turbocharged 90 degree V6 engine. In 2014, they appeared for the first time, and they have been further developed since then.
The FIA began negotiating in 2017 with existing constructors and potential new manufacturers about the next generation of engines, which was initially scheduled for introduction in 2021 but was delayed to 2022. In the original proposal, the goal was to simplify engine designs, cut costs, promote new manufacturers, and address criticisms launched against the 2014 generation. It proposed retaining the 1.6 L V6 configuration while abandoning the complex Motor Generator Unit-Heat (MGU-H) system.
What is the most powerful F1 engine ever?
The BMW M12/13/1 is the most powerful F1 engine ever made.
Power would drop to around 1,000 horsepower because boost levels were limited to ensure reliability during the race. The BMW M12/13/1 of 1986, which powered Benetton, Brabham, and Arrows, remains the most powerful engine to ever power a Formula 1 car.
Do all F1 cars have the same engine?
Cars are not the same. Each manufacturer makes their own car, and therefore one manufacturer might have a faster car than the other. Also, some teams are customers of other manufacturers when it comes to Power Unites. For example, Red Bull uses Honda engines, while McLaren uses Mercedes engines.
How fast is a Formula 1 car from zero to 60?
F1 cars accelerate from 0 – 60mph in roughly 2.6 seconds.
Although this might seem slow given their top speed, a majority of their speed comes from aerodynamics, which work more efficiently the faster the car goes, since they can’t unleash full power from a stop.
Do F1 cars use V12 engines?
No, F1 cars do not currently use V12 engines. The current engine formula for F1, which was introduced in 2014, requires teams to use turbocharged 1.6-liter V6 hybrid power units.
The last time V12 engines were used in F1 was in the 1995 season, when Ferrari used a 3.0-liter V12 engine in their 412T2 car.
Since then, F1 has transitioned to smaller, more efficient engines that use hybrid technology to improve performance while reducing fuel consumption and emissions.
Why are F1 engines so powerful?
F1 engines are so powerful because they are designed to produce as much horsepower as possible while still complying with strict FIA regulations.
The current engine formula for F1, which was introduced in 2014, requires teams to use turbocharged 1.6-liter V6 hybrid power units that can produce up to 1000 horsepower.
These engines use advanced technologies, such as turbocharging, direct fuel injection, and energy recovery systems, to maximize power output while minimizing fuel consumption and emissions.
F1 teams also invest heavily in engine development and optimization, using advanced simulation tools and testing facilities to fine-tune their engines for maximum performance. All of these factors combine to make F1 engines some of the most powerful and advanced engines in the world.
Does F1 have V8 engines?
F1 used to have V8 engines, but they are no longer used in the sport. The last time V8 engines were used in F1 was during the 2013 season, before the current turbocharged 1.6-liter V6 hybrid power units were introduced in 2014.
The V8 engines used in F1 were typically 2.4-liter naturally aspirated engines that could produce up to 750 horsepower. While they were less powerful than the current V6 hybrid power units, they still provided plenty of excitement and spectacle on the track.
However, F1 made the switch to the current engine formula to improve efficiency and sustainability, while still maintaining high levels of performance and excitement.
Why did F1 stop using V10?
F1 stopped using V10 engines because the FIA, the governing body of F1, wanted to reduce costs and improve efficiency in the sport.
In 2006, the FIA introduced new regulations that required teams to use 2.4-liter V8 engines instead of the more powerful and fuel-hungry 3.0-liter V10 engines that were previously used.
The decision to switch to V8 engines was made in part to reduce costs for the teams, as V8 engines were less expensive to develop and maintain than V10 engines. Additionally, the switch was intended to improve fuel efficiency and reduce emissions, which was becoming an increasingly important issue in the automotive industry.
While some fans and critics lamented the loss of the V10 engines, the switch to V8 engines ultimately helped to make F1 more sustainable and cost-effective in the long run.
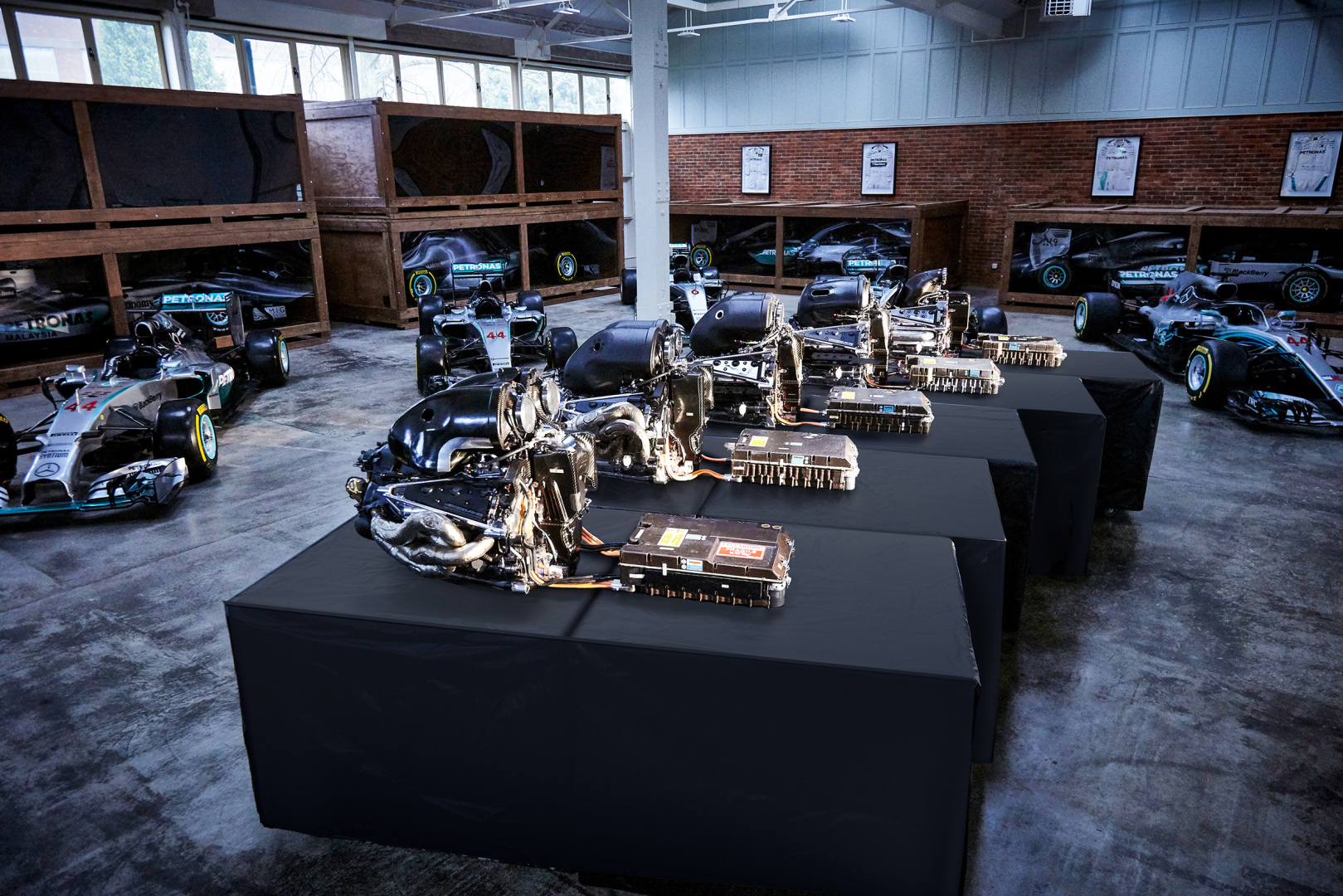