How Do F1 Teams Make Carbon Parts?
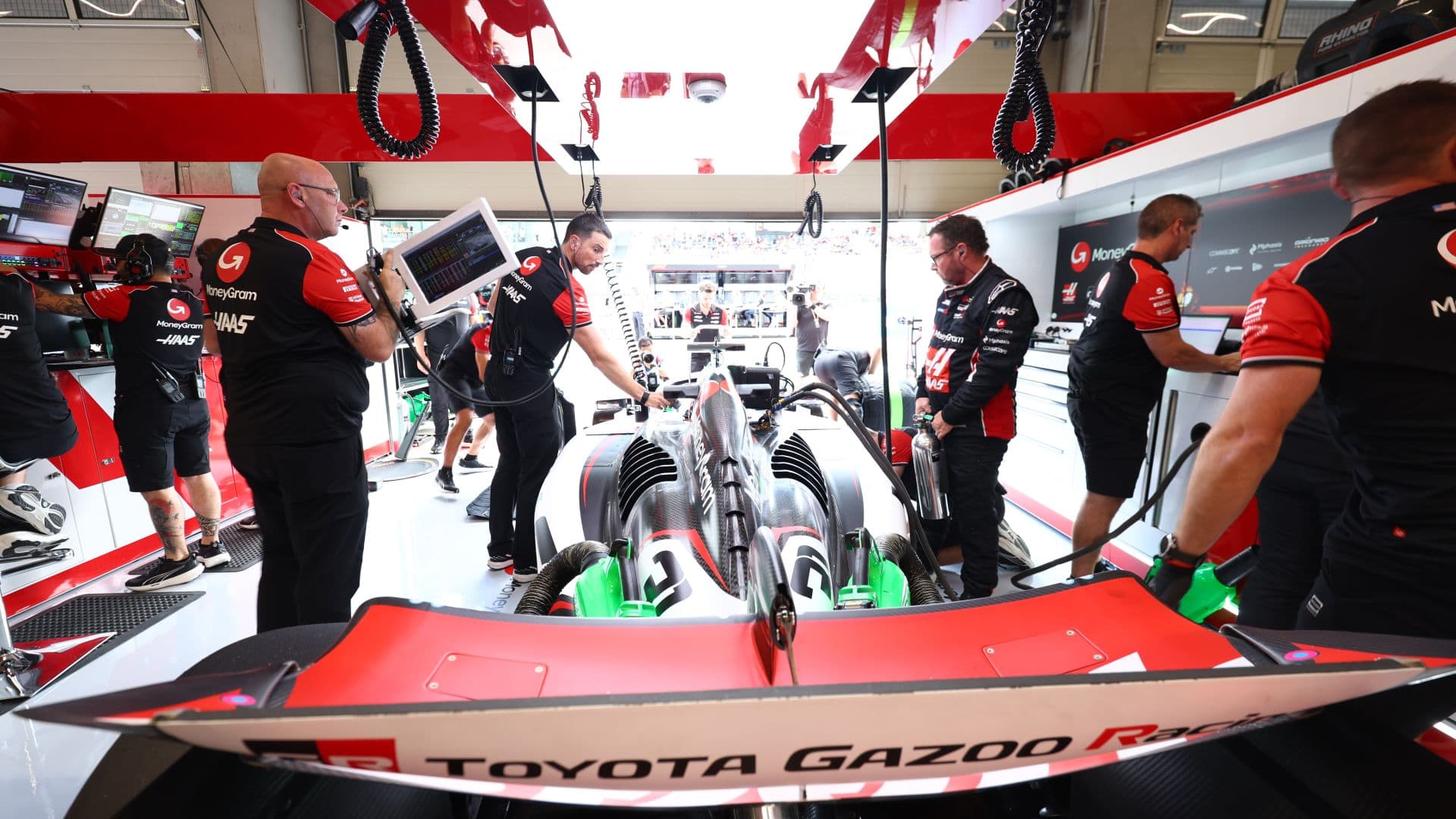
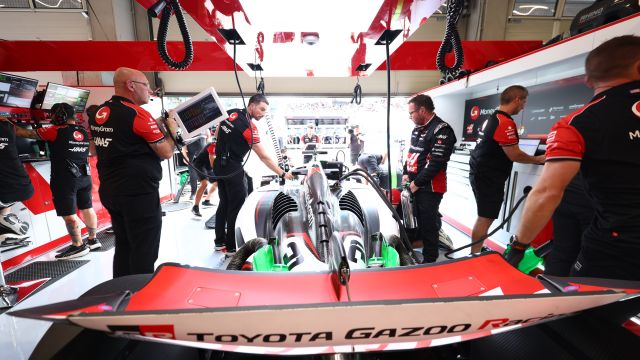
Formula 1 teams manufacture carbon fibre parts using a highly controlled process that begins with digital design and ends with autoclave curing. Most components are made from prepreg carbon fibre, which is layered into moulds, vacuum-sealed, cured under pressure and heat, then trimmed and tested before track use. Some parts can go from concept to installation in as little as 45 hours.
Carbon fibre is essential to modern F1. It combines low weight with extreme strength, making it ideal for everything from the chassis and wings to suspension arms and brake ducts. The parts must withstand high loads, temperatures, and aerodynamic forces while remaining light enough to optimise performance.
How is F1 carbon fibre made?
Formula 1 carbon fibre parts are made from prepreg sheets, pre-impregnated carbon fibres combined with resin, which are precision cut, layered into moulds, then cured in an autoclave under heat and pressure. This process creates rigid, lightweight components capable of withstanding extreme loads on track.
Prepreg carbon fibre: the foundation of F1 construction
F1 teams use prepreg carbon because it allows consistent resin content and precise control over strength, weight, and thickness. The material arrives in rolls and is stored at low temperatures to delay curing. Each sheet is cut to a specific shape using automated machines, following exact specifications from CAD models.
These pieces are then laid into moulds in a defined fibre orientation. The direction of each layer affects the strength and flexibility of the final part. Multiple layers are often used to reinforce specific stress zones.
Moulding, curing, and finishing
The mould, often made from carbon fibre itself, is shaped to match the final part. Once the prepreg is laid up, the mould is sealed inside a vacuum bag and placed in an autoclave. There, it cures under pressure (typically up to 6 bar) and heat (between 120°C and 180°C), solidifying the resin and bonding the fibres.
After curing, the component is cooled, removed from the mould, trimmed, inspected, and tested. Many teams can complete this process in under 48 hours. This speed allows them to deliver aerodynamic upgrades between races.
Do F1 teams make their own parts?
Formula 1 teams are required to design and manufacture key components of their cars in-house, but they are permitted to source other parts from suppliers or partner teams. This model allows teams to remain constructors while managing cost and complexity.
What must teams build themselves?
According to the FIA’s Technical Regulations, teams must design and own the intellectual property for all Listed Team Components (LTC). These include:
- The survival cell and primary roll structure
- Front impact structures
- Aerodynamic components
- The fuel tank sensor and fuel bladder
- Primary heat exchangers
- SECU team applications
Teams must be able to demonstrate full ownership and control of the design process for these parts. This is essential for competitive integrity and aligns with Formula 1’s status as a constructor-based championship.
What components can be shared or sourced?
The regulations allow for Transferable Components (TRC). These are parts that can be shared between teams, typically where technical partnerships exist. Examples include:
- Gearboxes and clutch systems
- Inboard suspension parts and uprights
- Power-assisted steering systems
- Exhaust systems beyond the turbine
- Certain hydraulic and fuel system components
For instance, Haas sources several components from Ferrari, while Red Bull and Visa Cash App Racing Bulls have expanded their collaboration to include more parts and shared infrastructure.
What about standardised parts?
There are also Standard Supply Components (SSC) that every team must use. These are supplied by a designated manufacturer to ensure parity across the grid. They include:
- The standard ECU and telemetry system
- Brake systems and tyre pressure monitors
- TV cameras, rear lights, and the accident data recorder
In addition, Open Source Components (OSC) are designs made available to all teams. These include parts like the steering column, DRS mechanism, and brake calipers.
Why this matters for carbon fibre parts
While most teams build their structural and aerodynamic carbon fibre components themselves to maintain competitive secrecy and performance, the broader parts ecosystem in F1 is a carefully regulated mix of independence and cooperation. Each component falls into a specific category, balancing innovation with cost control.
What type of carbon is used in F1?
Formula 1 teams use aerospace-grade carbon fibre composites, engineered for the highest levels of performance, stiffness, and weight savings. This carbon is vastly different from what’s used in consumer applications like bicycles or automotive trim. It must meet demanding mechanical properties, thermal resistance, and reliability under extreme loads.
Prepreg carbon fibre: The industry standard
Formula 1 teams primarily use high-grade aerospace carbon fibre, known for its exceptional strength-to-weight ratio, stiffness, and resistance to heat and stress. This carbon fibre is typically pre-impregnated with epoxy resin, known as “prepreg,” allowing precise control over fibre orientation and resin content during manufacturing.
Prepreg carbon sheets are cut, layered into moulds, and cured under high pressure and temperature in an autoclave. The result is a high-strength, low-weight laminate tailored to its application.
Key types of fibres and reinforcements
F1 teams use a variety of advanced fibres, including:
- Standard modulus fibres for general structural parts
- Intermediate and high modulus fibres where stiffness is prioritised (such as suspension components or aerodynamic vanes)
- Spread tow fabrics that reduce weight and improve surface finish
- 3K, 6K, or 12K tows, which refer to the number of filaments per bundle in the weave, affecting the balance of strength and flexibility
These fibres are combined with specially formulated epoxy resin systems designed for impact resistance, temperature stability, and high vibration environments.
High-modulus vs. standard-modulus carbon
F1 engineers select carbon fibre types based on their specific structural needs. High-modulus carbon fibre offers superior stiffness, making it ideal for parts that must resist flexing, such as the monocoque or suspension arms. Standard-modulus carbon fibre provides a balance between flexibility and strength and is more commonly used in bodywork or aerodynamic surfaces.
Unidirectional and woven fabrics
Carbon fibre for F1 parts comes in different weaves and orientations. Unidirectional prepreg has fibres aligned in one direction, allowing engineers to control strength along specific load paths. Woven carbon fibre, with fibres interlaced at angles, offers multidirectional strength and is often used in visible areas like bodywork and wings for both performance and visual appeal.
Thermal and impact considerations
Some components are made using hybrid materials, combining carbon fibre with aramid fibres such as Kevlar or Zylon. These materials enhance impact resistance and are often used in areas prone to debris strikes or crash loads. Zylon is also mandatory in certain cockpit structures to improve driver protection.
The carbon fibre used in F1 must meet exacting performance and safety standards. Supplied by specialist manufacturers, it is stored and handled under controlled conditions to preserve integrity before fabrication.
Sustainable alternatives emerging
While traditional carbon remains the performance benchmark, teams like McLaren have trialled natural fibre composites, such as flax-reinforced resin, in non-critical components to reduce environmental impact. Recycled carbon fibre is also under development, as F1 moves toward greater sustainability.
How carbon fibre parts are tested and validated
Before any carbon fibre component is fitted to a Formula 1 car, it undergoes rigorous testing to ensure safety, reliability, and performance under extreme conditions. These tests are a crucial part of the development cycle, confirming that a part will survive the demands of high-speed racing.
Simulations and modelling
The validation process begins in the virtual world. Engineers use finite element analysis (FEA) to simulate how each carbon fibre component will respond to various stresses. This includes torsion, compression, and shear forces, as well as the effects of heat, vibration, and fatigue over time. These digital simulations help optimise a part’s fibre layout and thickness before any material is physically manufactured.
Thermal modelling ensures the part can withstand the high temperatures produced by brakes, engines, and exhaust systems. Vibration testing helps predict how components respond to the constant oscillations of a moving F1 car, especially those mounted close to the suspension or power unit.
Real-world impact and fatigue testing
Once simulations are complete, the part is built and tested in real conditions. Static load tests replicate the stresses a part will face on the car. Engineers apply controlled pressure to key areas of the component and use strain gauges to measure deformation and verify that it remains within the safe range.
Crash simulations and impact tests are particularly important for safety-critical parts like the monocoque or front crash structure. These parts must absorb high amounts of energy without failing catastrophically, protecting the driver during an accident.
To ensure long-term durability, components also undergo lifecycle endurance testing. This mimics the wear and tear experienced across multiple race weekends, allowing teams to identify failure points and improve part longevity.
What were F1 cars made of before carbon fibre?
Before the introduction of carbon fibre in the early 1980s, Formula 1 cars were primarily constructed from aluminium alloys and, in earlier decades, steel tubing. These materials offered strength but at a significant weight penalty compared to modern composites.
Steel spaceframes: The early era
In the 1950s and 1960s, most Formula 1 cars used steel spaceframe chassis designs. These were made by welding steel tubes into a triangulated structure, providing reasonable rigidity and ease of repair. However, they were heavy and offered limited protection in crashes.
Aluminium monocoques: A major step forward
The late 1960s saw a shift to aluminium monocoque chassis, beginning with the revolutionary Lotus 25 in 1962. Instead of a tubular frame, the car used a lightweight aluminium shell with internal bracing, improving stiffness and reducing weight. This design became the standard in F1 for nearly two decades.
By the late 1970s, aluminium honeycomb structures were widely adopted, offering improved energy absorption and stiffness. These monocoques were stronger and lighter than steel frames but still lacked the performance potential of composite materials.
The carbon fibre revolution
Everything changed in 1981 when McLaren introduced the MP4/1, the first F1 car with a full carbon fibre monocoque. Designed by John Barnard, it immediately demonstrated a leap in crash protection and structural performance. The car’s survival of a high-speed crash at Monza that year validated the new material, and the rest of the grid followed suit.
Today, aluminium and steel are still used in secondary components or reinforcement points, but carbon fibre has become the defining material of modern Formula 1 construction.
Why is carbon fibre good for F1 cars?
Carbon fibre is ideal for Formula 1 cars because it combines high stiffness, strong tensile strength, low weight, excellent chemical resistance, and stability at high temperatures. These properties allow teams to build components that are incredibly strong yet lightweight, making the car faster, safer, and more efficient on track.
Lightweight construction boosts performance
A lighter car accelerates faster, brakes more effectively, and changes direction with greater agility. Carbon fibre weighs significantly less than traditional metals while offering superior structural strength, allowing engineers to lower a car’s overall weight without compromising safety.
Stiffness improves driver control
Carbon fibre resists flexing under stress, which improves chassis feedback and suspension precision. This stiffness enhances the driver’s ability to feel what the car is doing, particularly during high-speed cornering or sudden braking, making it easier to maintain control and maximise lap times.
Built-in crash protection
In the event of an accident, carbon fibre’s layered structure is designed to absorb and dissipate impact energy. Key safety features, including the monocoque (survival cell), wheel tethers, and cockpit protection devices like the halo, are all constructed using carbon fibre for its energy-absorbing capabilities.
Designed for aerodynamic advantage
The mouldability of carbon fibre enables aerodynamicists to sculpt bodywork with millimetre precision. Teams use this flexibility to optimise airflow, minimise drag, and generate the downforce needed to keep the car stable at speed.
Carbon fibre has transformed the design and performance of Formula 1 cars. Its unmatched strength-to-weight ratio, high thermal tolerance, and resistance to deformation make it the material of choice for everything from chassis construction to aerodynamic components. With strict FIA rules guiding what teams can and cannot build in-house, each carbon part is the result of a tightly controlled process involving digital simulations, autoclave curing, and rigorous testing.
As sustainability goals evolve and material science progresses, F1 teams continue to explore new ways to produce faster, safer, and more efficient cars. From flax-based components to recyclable fibres, the future of carbon composites in Formula 1 is as dynamic as the sport itself.
From F1 news to tech, history to opinions, F1 Chronicle has a free Substack. To deliver the stories you want straight to your inbox, click here.
For more F1 news and videos, follow us on Microsoft Start.
New to Formula 1? Check out our Glossary of F1 Terms, and our Beginners Guide to Formula 1 to fast-track your F1 knowledge.
F1 Carbon Parts FAQs
What are Formula 1 car parts made of?
Modern Formula 1 car parts are primarily made from advanced composite materials, especially carbon fibre. Other components may include aramid fibres like Kevlar, thermoplastic blends, and reinforced polymers. These materials offer a strong balance of light weight, rigidity, and energy absorption.
What is carbon fibre and why is it used in F1?
Carbon fibre is a composite material made of thin strands of carbon atoms woven into fabric and set in resin. It offers exceptional stiffness, tensile strength, chemical resistance, and low thermal expansion. In F1, it enables strong, lightweight structures that enhance speed, agility, and crash protection.
How thick is carbon fibre in F1 cars?
The thickness of carbon fibre parts in F1 varies by application. Most structural elements use laminates built from multiple thin plies, often totalling 2 to 6 millimetres. Heavily stressed areas, like the monocoque or suspension mounts, may be thicker for added strength.
How expensive is carbon fibre in Formula 1?
Carbon fibre is one of the most costly materials in motorsport. A single kilogram can cost hundreds of dollars, and a full chassis may cost upwards of $650,000 to produce. Each race weekend, teams may use several thousand dollars’ worth of carbon fibre on new parts and repairs.
Can F1 carbon fibre be recycled?
Yes, some teams and suppliers are developing ways to recycle carbon fibre. For example, McLaren trialled recycled carbon fibre at the 2023 United States Grand Prix. Recycled composites offer a more sustainable alternative while retaining some structural benefits of virgin material.
How much of an F1 car is made from carbon fibre?
Approximately 80% of an F1 car’s volume is made from carbon fibre or carbon composites. This includes the chassis, floor, wings, suspension components, and even driver safety elements like the cockpit halo and helmets.