Planes, Cranes, And Automobiles: F1’s Logistical Ballet From Bahrain To Australia
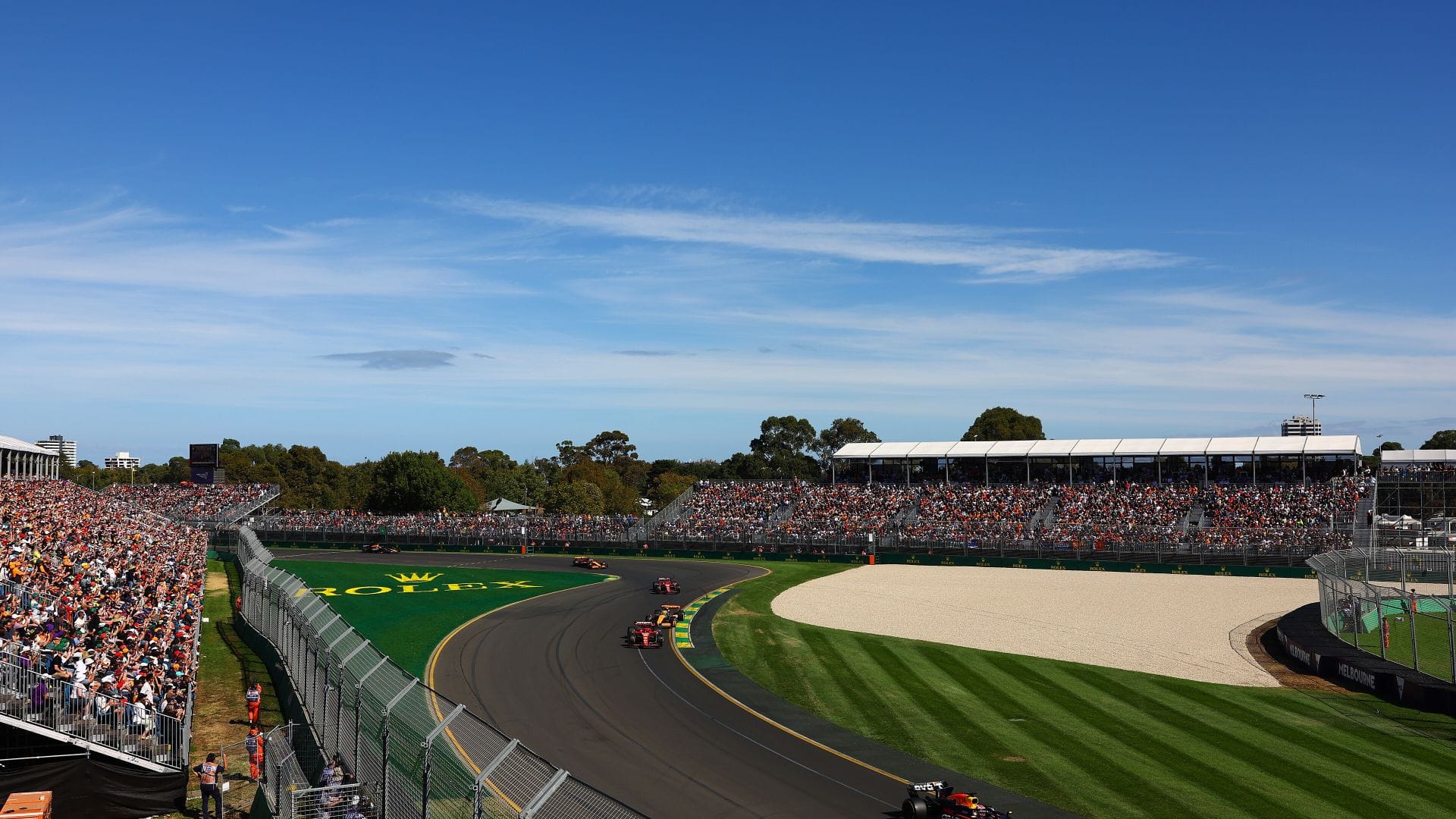

Getting from pre-season testing in Bahrain to the first race of the 2025 F1 season in Melbourne is a big logistical ask. The distance and the time between testing and the weekend mean teams have to be incredibly precise with their packing and planning.
Getting the cars, spares, and garage equipment from Bahrain to Melbourne involves a mix of air and sea freight and local transport in Melbourne, with teams needing to work closely with their logistics partners to navigate customs, optimise routes and develop contingency plans for any issues that might arise.
With just fourteen days between pre-season testing ending in Bahrain and the cars taking to the track at Albert Park, how will teams overcome this logistical nightmare? Let’s investigate…
Air Freight
Air freight is the primary means of transportation for Formula 1 teams’ most critical and time-sensitive equipment, including race cars, spare parts, and essential garage components, and it is the primary method for teams to get from Bahrain to Melbourne in time.
Teams typically rely on chartered cargo aircraft, such as the Boeing 747 or the Antonov An-124, which offer ample capacity and the ability to accommodate oversized items like car chassis and wings. The total volume of air freight per team can range from 30 to 50 tons, with the cars themselves weighing approximately 1,250 pounds (567 kg) each when fully assembled.
To ensure the safe and secure transportation of their equipment, teams use specially designed air freight containers that are purpose-built to protect the delicate components during transit. These containers feature custom padding, shock absorbers, and climate control systems to maintain optimal conditions for the sensitive electronics and composite materials used in modern Formula 1 cars.
The timeline for air freight transportation is tight, with teams aiming to have their equipment arrive in Melbourne no later than two to three days before the start of the race weekend. This allows sufficient time for customs clearance, delivery to the Albert Park circuit, and setup of the garage facilities. Teams work closely with their logistics partners to coordinate the loading and unloading of the aircraft, as well as to manage the necessary documentation and permits required for international shipments.
To optimise the air freight process, teams often employ a “fly-away” kit strategy, which involves sending a smaller subset of essential equipment ahead of the main shipment. This kit typically includes the most critical spare parts, tools, and electronics needed to prepare the cars for the race weekend, allowing teams to begin their setup and preparation work while the remainder of their equipment is still in transit.
Local Transportation
Local transportation involves the movement of teams’ equipment from the port of entry in Melbourne to the Albert Park circuit. This process relies on a fleet of trucks and trailers to transport the vast array of items needed for a successful race weekend.
The primary challenge of heavy logistics lies in the sheer volume and variety of equipment that needs to be moved. Teams require multiple 40-foot shipping containers to transport their gear, which can include everything from garage equipment and spare parts to hospitality units and marketing materials. The containers are loaded onto flatbed trailers or curtain-sided trucks, depending on the specific requirements of the equipment being transported.
To manage the complexities teams work with local transportation providers who have experience in handling the unique demands of Formula 1. These providers are responsible for ensuring that the trucks and trailers meet the necessary safety and security standards, as well as for providing skilled drivers who are familiar with navigating the local roads and traffic conditions in Melbourne.
The timing is critical, as teams must balance the need for early delivery to allow for sufficient setup time against the cost and availability of storage space at the circuit. In most cases, teams aim to have their equipment delivered to the Albert Park circuit two to three days before the start of the race weekend. This allows them to begin the process of unloading, unpacking, and setting up their garage and hospitality facilities.
Once the race weekend is concluded, the process is reversed, with teams packing up their equipment and loading it back onto trucks and trailers for transportation to the port of exit. The efficiency of this post-race logistics operation is crucial, as teams must quickly transition to the next race on the calendar, often with limited time between events.
Logistics Partners
Logistics partners play a vital role in the smooth operation of all Formula 1 teams, particularly when it comes to managing the complex task of moving equipment and personnel around the world. These partners, such as DHL, UPS, and FedEx, offer specialised services tailored to the unique needs of the motorsport industry.
One of the primary responsibilities of logistics partners is to handle the customs clearance process for teams’ equipment. This involves navigating the complex web of international regulations and documentation requirements, ensuring that all items are properly declared and that any necessary duties and taxes are paid. Logistics partners employ dedicated customs experts who work closely with teams to streamline this process, minimising the risk of delays or complications.
In addition to customs clearance, logistics partners also provide comprehensive tracking and monitoring services for teams’ shipments. This includes the use of advanced GPS tracking systems and sensor technologies that provide real-time visibility into the location and status of each container or package. By monitoring factors such as temperature, humidity, and shock, logistics partners can ensure that sensitive equipment remains in optimal condition throughout the shipping process.
Logistics partners also offer a range of value-added services to support teams’ operations at the track. This can include the provision of on-site logistics coordinators who work closely with team personnel to manage the delivery and collection of equipment, as well as the coordination of any last-minute shipments or special requests. Some logistics partners even offer specialised packaging solutions, such as custom-built flight cases or foam inserts, to provide an extra level of protection for high-value components.
To ensure the highest level of service, logistics partners often dedicate specific teams or divisions to focus exclusively on Formula 1 and other motorsport clients. These specialised teams have a deep understanding of the unique challenges and requirements of the industry, allowing them to provide tailored solutions that meet the precise needs of each team.
The importance of reliable and efficient logistics partners cannot be overstated in the fast-paced world of Formula 1. By entrusting their shipping and logistics needs to these experts, teams can focus on their core competency—developing and racing their cars—while having the confidence that their equipment will arrive at each race on time and in perfect condition.
F1 Transport And Sustainability
In their pursuit of sustainability, Formula 1 teams are actively working with logistics partners to minimise the environmental impact of their operations. One key strategy is the use of biofuels for air freight, which can significantly reduce carbon emissions compared to traditional jet fuel. For example, the use of sustainable aviation fuel (SAF) derived from waste materials or algae can result in up to an 80% reduction in greenhouse gas emissions over the fuel’s life cycle.
Teams are also exploring the use of more efficient aircraft for their cargo shipments. The Boeing 747-8F, for instance, offers a 16% improvement in fuel efficiency and a 16% reduction in carbon emissions compared to its predecessor, the 747-400F. By optimising their choice of aircraft and fuel, teams can make significant strides in reducing the carbon footprint of their logistics operations.
The use of reusable and recyclable packaging is another key aspect of sustainability in Formula 1 logistics. Teams are investing in high-quality, durable flight cases made from materials such as aluminium and carbon fibre, which can withstand the rigours of multiple international shipments. By using these reusable containers, teams can significantly reduce their reliance on single-use packaging materials, such as plastic wrap and foam inserts.
Logistics partners are also working with teams to implement comprehensive recycling programs at the track. This involves providing clearly marked waste bins for different materials, such as plastic, paper, and metal, and ensuring that all waste is properly sorted and processed. In some cases, logistics partners may even work with local recycling facilities to ensure that materials are recycled or repurposed in an environmentally friendly manner.
The tight turnaround between the Australian and Chinese Grands Prix poses an additional challenge for teams looking to minimise their environmental impact. With just one week between the two races, teams must rely on a combination of air and sea freight to ensure that their equipment reaches Shanghai in time for the event.
To optimise this process, teams may choose to send a portion of their equipment, such as garage infrastructure and hospitality units, by sea freight in advance of the Australian Grand Prix. This allows them to reduce the volume of cargo that needs to be flown directly to Shanghai, minimising both costs and carbon emissions. However, this approach requires careful planning and coordination to ensure that all necessary equipment arrives at the track in time for the race weekend.
As the 2025 Formula 1 season progresses, teams will continue to face complex logistical challenges as they navigate the global calendar. By prioritising sustainability and working closely with their logistics partners, they can minimise their environmental impact while still maintaining the highest levels of performance on the track. The successful implementation of sustainable practices during the transition from Bahrain to Melbourne and on to Shanghai will serve as a model for the rest of the season, showcasing the sport’s commitment to responsible and efficient logistics operations.