What Is A Monocoque?
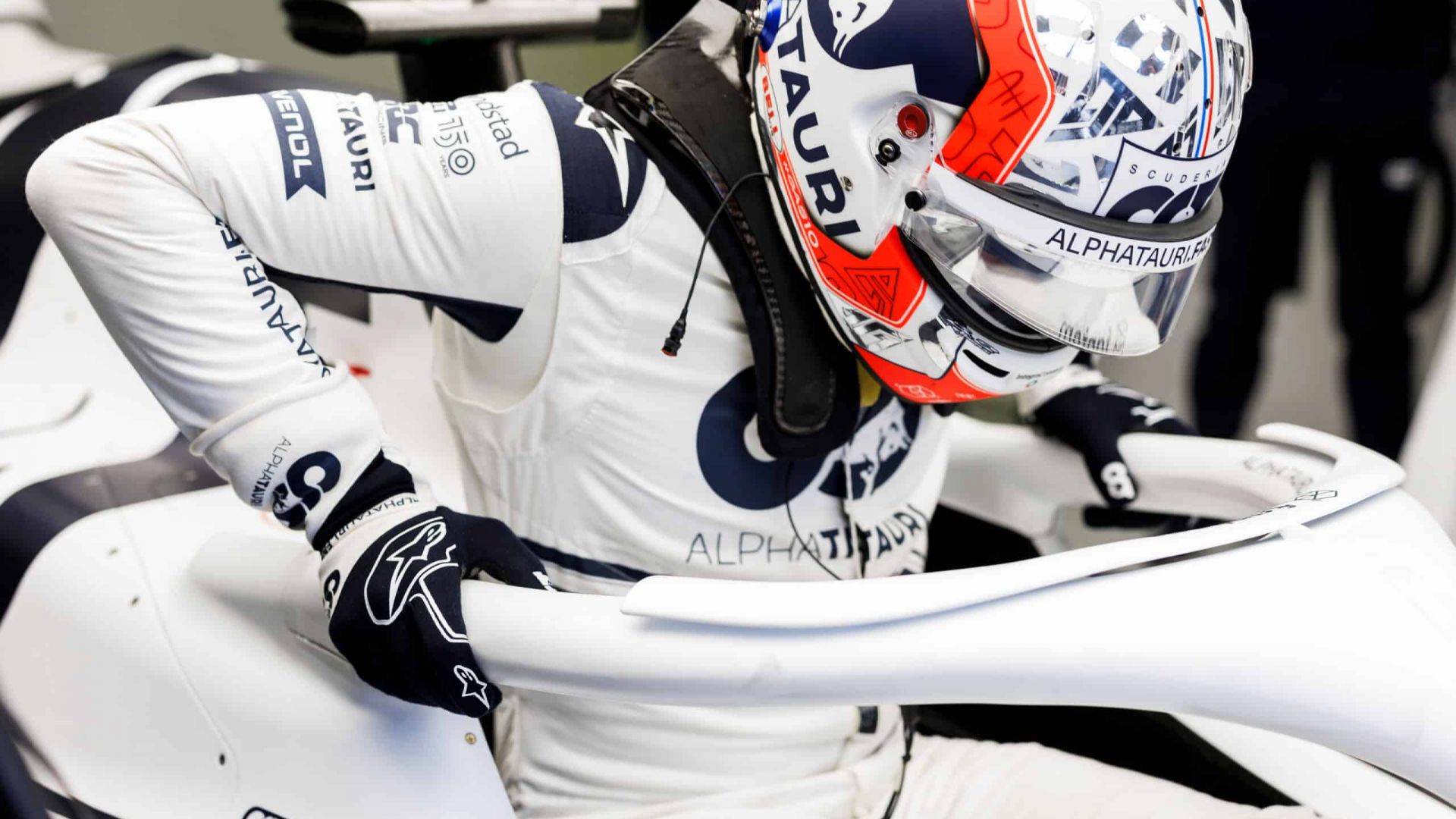
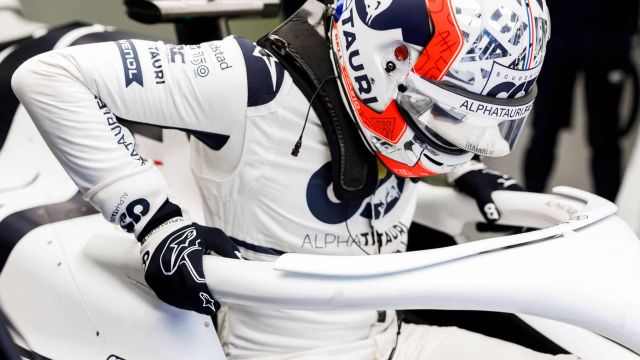
The word monocoque is a French word and means a single cell. Monocoque is derived from the Greek words: “mono” for single and “coque” for cell. In Formula 1, monocoque refers to the “survival cell” that protects the Formula 1 car driver.
In Formula 1, a monocoque chassis is a single-shell structure that integrates the cockpit and primary load-bearing elements into one rigid unit. Constructed primarily from carbon fibre composites, it provides exceptional strength-to-weight ratio, crucial for driver safety and aerodynamic efficiency.
Unlike traditional ladder or spaceframe chassis, the monocoque design evenly distributes impact forces, enhancing structural integrity and crash protection.
Mandated by the FIA, modern F1 monocoques undergo extensive crash testing to meet stringent safety regulations while optimising vehicle dynamics and torsional rigidity.
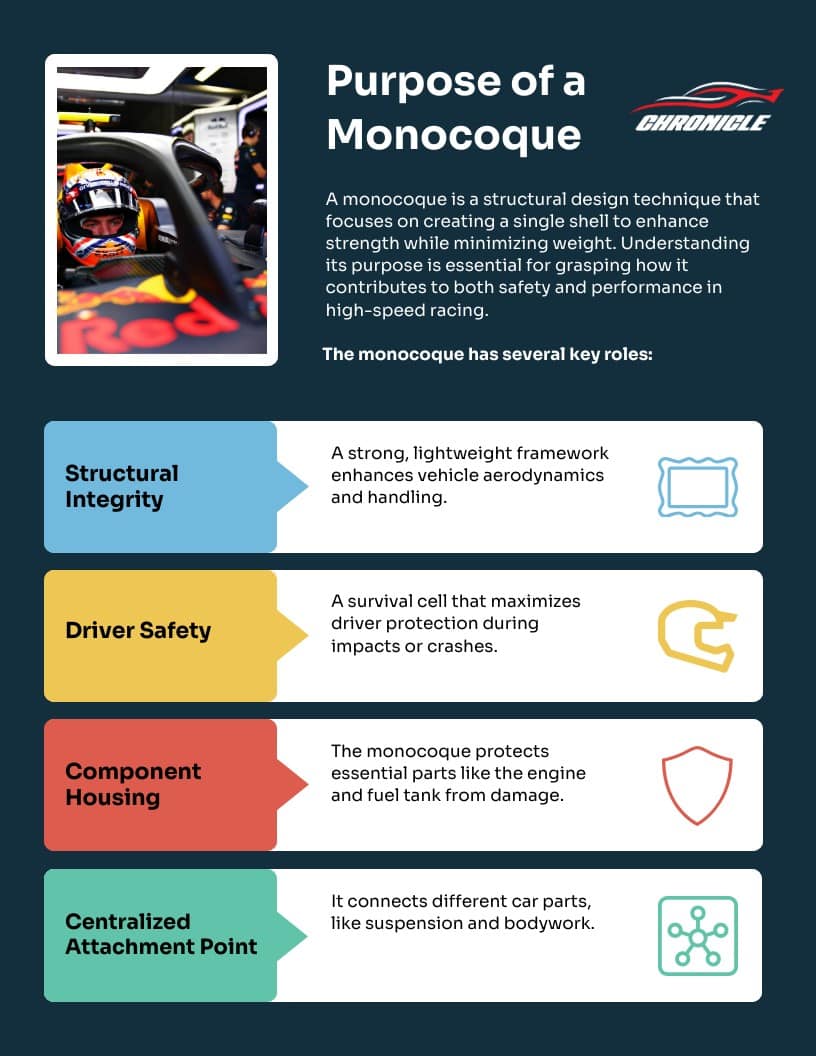
What is an F1 monocoque?
With the improvement in engines and the speeds of Formula 1 cars, incidents were also on the rise on race tracks. The risk to Formula 1 drivers, race officials as well as spectators was also increasing. Injuries and casualties also increased highlighting the risk to personnel involved with a Grand Prix. The FIA and constructors of Formula 1 cars decided to make cars as safe as possible for all concerned. The aim was to minimise risk to the drivers by limiting the damage caused by an impact and keeping the debris emanating from an incident to a minimum. This move was to greatly improve the safety of personnel involved with racing.
The Lotus team designer and boss Colin Chapman was the first man to use a monocoque in a Formula 1 car. Conventionally a tubular aluminium space frame was used in the construction of Formula 1 cars. Chapman used a riveted lightweight metal case instead of a tubular frame in the Lotus 25 in 1962. That was the first instance of the use of a monocoque in a Formula 1 car. The experiment was highly successful. Teams took Chapman’s lead and started researching with various materials to construct a monocoque.
In 1981, McLaren came out with a carbon fibre safety cell in their Formula 1 car. Lotus started research on composites of carbon and kevlar reinforced resin. They used the “cut and fold” methodology that would replace the pre-bonded aluminium skins in Formula 1 cars. McLaren was simultaneously conducting research on carbon fibre composites. In 1983, McLaren rolled out the MP4/1C, the first Formula 1 car with a carbon fibre moulded monocoque. The credit for designing and constructing the monocoque goes to McLaren’s main engineer, John Barnard. Although the car was originally powered by a Ford engine, McLaren later shifted to a Porsche engine. Hercules Aerospace constructed the first monocoque for McLaren.
How is a car monocoque made?
The earlier monocoques were built on two male moulds. McLaren used alternate carbon fibre layers that were interspaced with alloy honeycombs. Lotus used folded composite carbon fibre sheets in layers. The two moulds were later bonded together at the bulkheads to form the monocoque. The use of male moulds meant that the outer surface had a rough finish. But this method was adopted so that the suspension mounting points could be accurately placed. The chassis was strong and withstood the impact forces very well.
Carbon composites proved to be very resilient and constructors were satisfied with the material, and all teams soon started experimenting with carbon composites to build a monocoque.
In 1983, the ATS team experimented with a new way of fabricating the monocoque. They used a female mould to construct the two halves of the monocoque. The result was a monocoque with a much smoother finished outer surface. With a neater surface, ATS were able to discard the outside bodywork altogether. The car was much lighter after doing away with the outside shell of the car. Ferrari was not far behind in following this method of moulding the monocoque. The Ferrari 126C3 was built with a full carbon-composite chassis.
The advent of advanced aerodynamics meant cars started having more complex shapes. By 2000. The mould was broken into several sections or parts. These were all bonded together to form the monocoque. All teams resorted to carbon composite monocoques for their added resilience and safety. Research and experimentation on composites yielded materials with better resilience and impact withstanding capacity. The composite now used in monocoques is twice as strong as steel but five times lighter.
All the sections of a monocoque are handmade. Twelve layers of carbon fibre mats are placed, one over the other, in a mould. A carbon fibre mat is made from very fine interwoven threads. Each of these threads is five times thinner than human hair. Depending on the anticipated loads on each section, mats with different weave patterns are used in different moulds. To increase the rigidity of the monocoque, a honeycomb-patterned aluminium layer is inserted between two carbon mats.
The shell is then heated in an autoclave. An autoclave is a giant oven under negative pressure. It takes two and a half hours of heating at a predetermined temperature before the shell gets hardened. This procedure is repeated twice more to season the shell. This makes the shell strong and resilient enough to protect drivers in very severe accidents. When Giancarlo Fisichella crashed his car at the 1997 Silverstone Grand Prix, he walked away with only a minor knee injury. An analysis of the Accident Data Recorder (black box) later showed that his car came to a stop from 227km/h in only 0.72 seconds.
Technical Advancements
Over the years, Formula 1 teams have continuously pushed the boundaries of monocoque design and materials to enhance performance and driver safety. One of the most significant advancements has been the widespread adoption of carbon fibre-reinforced polymers (CFRPs). CFRPs offer an exceptional strength-to-weight ratio, allowing teams to construct lighter yet stronger monocoques. This has been achieved through advancements in manufacturing processes, such as the use of high-precision layering techniques and autoclave curing, which ensure optimal alignment and bonding of the carbon fibres.
Recent innovations in monocoque technology include the integration of honeycomb structures within the CFRP layers. These honeycomb structures, typically made from lightweight materials like aluminium or Nomex, provide additional crush resistance and energy absorption during impacts. By strategically placing these honeycomb layers in areas prone to high stress, such as the side pods and nose section, teams have further enhanced the overall integrity of the monocoque.
Another area of advancement is the development of multi-directional CFRP layering. By orienting the carbon fibers in various directions, engineers can optimize the monocoque’s strength and stiffness in specific areas. This allows for better load distribution and improved handling characteristics, as the monocoque can more effectively resist twisting and bending forces encountered during high-speed cornering and braking.
Some F1 teams have also experimented with the integration of other advanced materials into the monocoque construction. For example, McLaren has incorporated titanium inserts in high-stress areas to improve structural integrity while minimizing weight. Ferrari, on the other hand, has explored the use of graphene, a single-layer carbon material with exceptional strength and stiffness properties, to enhance the performance of their monocoques.
Advancements in simulation and modelling technologies have allowed teams to optimise monocoque designs virtually before physical manufacturing. Finite Element Analysis (FEA) and Computational Fluid Dynamics (CFD) simulations enable engineers to predict the behaviour of the monocoque under various loading scenarios, identifying potential weak points and refining the design accordingly. This virtual testing process has not only accelerated the development cycle but also reduced the need for expensive physical prototypes.
What tests are F1 monocoques subject to?
The FIA as well as the Formula 1 teams are tirelessly working to improve the safety of Formula 1 drivers. A monocoque made from carbon fibre composites can be as light as 35kg. Yet it tolerates fantastic cornering speeds, aerodynamic loads and very large impact loads. The FIA, along with team designers, have formulated several new rules that have to be followed before a monocoque is accepted for use. The FIA mandated several crash tests in 1985. These tests are obligatory and are getting more stringent by the year.
Crash tests for rear and side crash structures as well as rollover bar have been made mandatory since 1997. These tests are carried out before the beginning of each new season. The tests are conducted in front of an FIA delegate according to procedures laid down by the FIA. All the measuring instruments used in a crash test are calibrated before the tests. To improve safety in the sport, the FIA continuously revises the standards to be met during these tests. The requirements to be met, increase in severity every season as the speeds of the cars increase.
Carbon fibre composites can withstand great dynamic loads. The FIA is concerned about the composites’ ability to withstand penetration. For this reason, the FIA made it mandatory that the inside most layer of the monocoque be made from Kevlar. Kevlar is a strong material and is highly resistant to penetrative forces or point dynamic loads. The mandate came after Michael Schumacher’s 1999 crash at Silverstone. The front suspension wishbone had penetrated Schumacher’s car and broken his leg.
The impact absorption capacity of a monocoque is measured in Specific Energy Absorption (SEA) units. These units are measured in kJ per kg a material can withstand. The SEA of composites is far higher than their metal counterparts. The SEA of steel and aluminium are 12kJ/kg and 20kJ/kg respectively. A monocoque is a highly refined and optimised structure made of carbon fibre reinforced polymer (CFRP). It can withstand impacts from 40kJ/kg to 70kJ/kg. That is the reason CFRPs are materials of choice for constructing monocoques.
A driver sits inside a monocoque in a cramped space. To ensure that a driver is as comfortable as he can be, the FIA has imposed limitations on the dimensions of the monocoque. The FIA specifies minimum inside dimensions to ensure the driver’s legs do not get injured. There are both maximum and minimum dimensional limits for the outside of the monocoque depending on the portion. While some portions are limited by maximum dimensions, others are constrained by minimum. This is to prevent aerodynamic engineers from getting carried away with the design of the car.
Impact on Driver Safety
The introduction of monocoque structures in Formula 1 has revolutionized driver safety, providing a robust and resilient survival cell that shields drivers from the extreme forces experienced during high-speed crashes. The monocoque’s ability to absorb and dissipate impact energy has been instrumental in reducing the risk of serious injuries and fatalities in the sport.
One of the most notable examples of the monocoque’s effectiveness in protecting drivers occurred during the 1981 Italian Grand Prix. John Watson, driving for McLaren, suffered a severe crash when his car hit the barriers head-on at a speed of approximately 140 mph (225 km/h). Despite the violent impact, Watson emerged from the wreckage with only minor injuries, a testament to the strength and integrity of the carbon fibre composite monocoque.
Since then, there have been numerous incidents where the monocoque has played a crucial role in saving drivers’ lives. In the 2002 Austrian Grand Prix, Takuma Sato’s Jordan car experienced a rear suspension failure, causing him to lose control and slam into the barriers at high speed. The monocoque absorbed the brunt of the impact, allowing Sato to walk away unscathed. Similarly, during the 2009 European Grand Prix, Mark Webber’s Red Bull car collided with Heikki Kovalainen’s McLaren, resulting in a spectacular somersault. Once again, the monocoque’s structural integrity ensured that Webber escaped without serious injuries.
To ensure that monocoques meet stringent safety standards, the FIA (Fédération Internationale de l’Automobile) mandates a series of rigorous crash tests before a car is deemed fit to compete. These tests simulate various impact scenarios, such as frontal, side, and rear collisions, as well as roll-over incidents. The monocoque must demonstrate its ability to maintain survival space for the driver and absorb impact energy effectively.
Over the years, the FIA has continuously evolved and strengthened these crash test requirements to keep pace with the increasing speeds and performance of Formula 1 cars. The frontal impact test, for example, now requires the monocoque to withstand a 60 kph (37 mph) impact with a 780 kg (1,720 lbs) striking plate, simulating a head-on collision with a stationary object. Similarly, the side impact test involves a 780 kg (1,720 lbs) impactor striking the monocoque at a speed of 50 kph (31 mph), ensuring the driver’s survival in the event of a side-on crash.
In addition to the structural integrity of the monocoque, other safety features have been integrated into its design to further enhance driver protection. The inclusion of side-impact structures, such as honeycomb panels and energy-absorbing foams, helps dissipate the energy of lateral impacts. The cockpit rim has also been reinforced to prevent foreign objects from penetrating the survival cell, a measure introduced after Felipe Massa’s accident in 2009 when a suspension spring struck his helmet.
The monocoque’s impact on driver safety extends beyond its ability to withstand crashes. Its design also incorporates features that improve the driver’s positioning and restraint within the cockpit. The seat and safety belts are securely anchored to the monocoque, ensuring that the driver remains firmly in place during high-speed manoeuvres and accidents. The headrest and neck support structures are also integrated into the monocoque, providing additional protection against head and neck injuries.
From F1 news to tech, history to opinions, F1 Chronicle has a free Substack. To deliver the stories you want straight to your inbox, click here.
New to Formula 1? Check out our Glossary of F1 Terms, and our Beginners Guide to Formula 1 to fast-track your F1 knowledge.
Monocoque FAQs
What is the purpose of a monocoque?
The purpose of a monocoque in Formula 1 is to:
- Provide a strong and lightweight structural framework for the car
- Serve as a survival cell to protect the driver in the event of a crash
- House and safeguard critical components, such as the engine, transmission, and fuel tank
- Act as a central point for attaching other parts of the car, like the suspension and bodywork
What is the difference between a monocoque and a chassis?
In Formula 1, the terms “monocoque” and “chassis” are often used interchangeably. However, there is a slight difference:
- A monocoque specifically refers to a single-shell structure that integrates the cockpit and the structural framework of the car
- A chassis, in a broader sense, encompasses the entire structural framework of the car, including the monocoque and other components like the front and rear subframes
What is an example of a monocoque?
An example of a monocoque in Formula 1 is the survival cell of a modern F1 car. It is constructed using carbon fibre-reinforced polymers (CFRPs) and is designed to:
- Provide a strong and rigid structure to protect the driver
- Absorb and dissipate impact energy during a crash
- Meet the strict crash test requirements set by the FIA
- Integrate with other components of the car, such as the suspension and power unit
What is the difference between monocoque and space frame chassis?
The main differences between a monocoque and a space frame chassis are:
Monocoque:
- Single-shell structure that integrates the cockpit and the structural framework
- Made from carbon fibre reinforced polymers (CFRPs) in modern Formula 1 cars
- Provides a strong, lightweight, and protective structure for the driver
- Requires complex manufacturing processes, such as layering and autoclave curing
Space frame chassis:
- Consists of a lattice-like structure made from interconnected tubes
- Typically made from steel or aluminium alloys
- Offers good structural strength but is generally heavier than a monocoque
- Easier to manufacture and repair compared to a monocoque
- Commonly used in older Formula 1 cars and other motorsport categories
In modern Formula 1, the monocoque design has largely replaced the space frame chassis due to its superior strength-to-weight ratio, improved driver protection, and the ability to integrate with other advanced components of the car.