What Chassis Do F1 Cars Use?

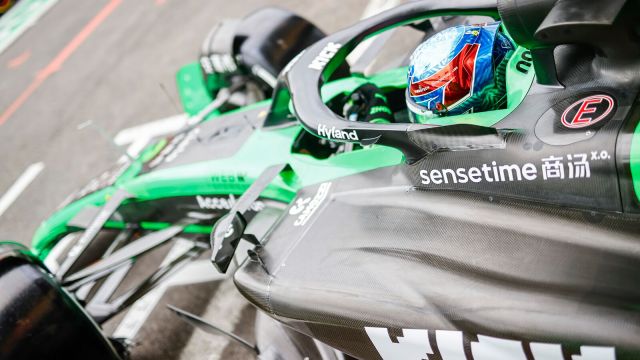
Formula 1 cars utilize highly specialized chassis designs crafted for maximum performance and safety. These advanced structures form the core of each F1 vehicle, integrating cutting-edge materials and engineering techniques. The primary chassis type used in modern F1 cars is a carbon fibre monocoque, which provides exceptional strength-to-weight ratio and rigidity.
F1 chassis designs constantly evolve to meet changing regulations and performance demands. Teams invest significant resources into chassis development, seeking advantages in aerodynamics, weight distribution, and driver protection. The chassis serves as the foundation for attaching crucial components like the engine, suspension, and bodywork.
Safety remains a top priority in F1 chassis design. Strict regulations govern chassis construction to protect drivers during high-speed impacts. Features like energy-absorbing structures and reinforced cockpit areas are integrated into every F1 chassis, showcasing the sport’s commitment to driver welfare alongside performance.
History of Chassis Evolution in Formula One
Formula One chassis design has undergone significant transformations since the sport’s inception. These changes have driven improvements in performance, safety, and aerodynamics.
From Spaceframe to Monocoque
Early F1 cars used spaceframe chassis, consisting of welded steel tubes. This design offered strength and rigidity while keeping weight low. The backbone chassis, a robust automotive design connecting the front and rear suspension attachment areas through a strong tubular structure, was also used historically in small sports cars and some heavy trucks. The Ferrari 500, which dominated the 1952 and 1953 seasons, featured a spaceframe chassis.
In the 1960s, teams began experimenting with monocoque construction. Colin Chapman’s Lotus 25, introduced in 1962, pioneered this technology in F1. The monocoque chassis used a single piece of material to form the main structure, improving rigidity and reducing weight.
Monocoque designs quickly became the standard in F1. They allowed for better integration of aerodynamic elements and enhanced driver safety. Teams refined these designs throughout the 1970s and 1980s, using materials like aluminum to further reduce weight.
Emergence of Carbon Fiber Technology
The 1980s saw a revolution in F1 chassis design with the introduction of carbon fiber composites. McLaren’s MP4/1, debuted in 1981, was the first F1 car to use a carbon fiber monocoque. Carbon fibres are produced using various precursor feedstocks such as rayon, pitch, and polyacrylonitrile, and their properties are enhanced through heat treatment, making them essential for modern Formula One car construction.
Carbon fiber offered several advantages:
- Higher strength-to-weight ratio than metal
- Better energy absorption in crashes
- Ability to create complex shapes for aerodynamics
By the mid-1980s, most F1 teams had adopted carbon fiber chassis. This material allowed designers to create stiffer, lighter, and safer cars. It also enabled the integration of aerodynamic elements directly into the chassis structure.
Carbon fiber technology continues to evolve in F1. Teams now use advanced manufacturing techniques to optimize chassis design for performance and safety. Modern F1 chassis are highly sophisticated structures, tailored to meet the sport’s demanding requirements.
Fundamentals of F1 Car Chassis Design
F1 car chassis design revolves around creating a lightweight yet strong structure that forms the primary load bearing member of the vehicle. The chassis must provide a rigid platform for mounting components while optimizing aerodynamics and safety.
Primary Load Bearing Structures
The monocoque chassis serves as the main load-bearing structure in modern F1 cars. Made from carbon fiber composites, it forms a single shell that integrates the cockpit and fuel tank. This design offers excellent strength-to-weight ratio and crash protection.
Carbon fiber’s high stiffness allows engineers to create complex shapes that enhance aerodynamics. The monocoque connects to the engine and gearbox, which also act as stressed members of the chassis. Together, these components form a cohesive unit that handles the immense forces experienced during racing.
Regulations stipulate minimum weight and dimensional requirements for the chassis. The FIA, the governing body of Formula 1, sets the minimum weight and dimensional requirements for F1 chassis to ensure safety and fairness. For the 2023 season, the key requirements were as follows:
- Minimum weight:
- The minimum weight of the car, including the driver and fuel, must be 798 kg (1,759 lbs).
- Chassis dimensions:
- Width: The overall width of the car must not exceed 2,000 mm (78.7 inches).
- Height: The height of the chassis must be at least 625 mm (24.6 inches) from the ground.
- Wheelbase: The distance between the front and rear wheel centers must be between 3,400 mm (133.9 inches) and 3,600 mm (141.7 inches).
- Front wing: The front wing width is limited to 2,000 mm (78.7 inches).
- Rear wing: The rear wing width is limited to 1,050 mm (41.3 inches), with a maximum height of 820 mm (32.3 inches) above the reference plane.
These dimensions are just a part of the comprehensive technical regulations that teams must adhere to when designing and constructing their chassis. The regulations cover various aspects of the car, including aerodynamics, safety features, and materials used.
Maximizing Structural Stiffness
A stiff chassis improves handling by allowing the suspension to work more effectively. Engineers use advanced simulation tools to analyze and refine the chassis design, identifying areas to add reinforcement or remove excess material.
Strategic use of high-modulus carbon fibers in key load paths increases rigidity without adding significant weight. Honeycomb structures sandwiched between carbon fiber layers further enhance stiffness in certain areas.
Torsional rigidity is particularly important, as it affects the car’s responsiveness to steering inputs. Designers aim to create a chassis that twists as little as possible under cornering loads.
The integration of aerodynamic elements like wings and floor with the chassis structure requires careful consideration to maintain stiffness while achieving desired airflow characteristics.
Materials Used in F1 Chassis Fabrication
F1 chassis construction relies heavily on advanced materials to achieve optimal performance. The relevance of spaceframe chassis design in high performance sports cars is crucial, as it provides a lightweight yet rigid structure essential for enhancing acceleration and maintaining control during races. These materials provide the necessary strength while minimizing weight.
Advantages of Carbon Fiber
Carbon fiber is the primary material used in F1 chassis fabrication. Its high strength-to-weight ratio makes it ideal for racing applications. Carbon fiber offers excellent stiffness and durability, allowing engineers to create lightweight yet rigid structures.
The material’s versatility allows for complex shapes and designs, enabling aerodynamic optimization. Carbon fiber also exhibits good energy absorption properties, enhancing driver safety during impacts. Its resistance to fatigue and corrosion contributes to the longevity of F1 chassis components.
Composite Materials and Honeycomb Structures
F1 chassis construction incorporates various composite materials alongside carbon fiber. These include kevlar and aramid fibers, which add specific properties to different chassis sections. Composite layups are carefully designed to provide directional strength where needed.
Honeycomb structures play a key role in F1 chassis design. These lightweight cores, often made of aluminum or nomex, are sandwiched between carbon fiber layers. The resulting structure offers exceptional stiffness and strength with minimal weight. Honeycomb cores also enhance energy absorption, further improving safety.
Engineers fine-tune the combination of materials and structures to meet specific performance requirements for each chassis section. This approach allows for precise control over mechanical properties throughout the car.
Safety Features Integrated into the Chassis
F1 car chassis incorporate advanced safety elements to protect drivers during high-speed racing. These features focus on structural integrity and impact resistance.
Increasing Torsional Rigidity for Safety
F1 chassis designs prioritize torsional rigidity to enhance driver protection. Carbon fiber composites form the core structure, offering exceptional strength-to-weight ratios. Engineers strategically place reinforcements at key stress points to absorb and distribute impact forces.
Monocoque construction creates a single-piece survival cell around the driver. This design minimizes flex and deformation during crashes. Crash tests validate the chassis’ ability to withstand severe impacts without compromising the cockpit area.
Resistance to External Intrusion
F1 chassis incorporate multiple layers of protection against external intrusions. Side impact structures absorb energy from lateral collisions. These honeycomb-style structures crush progressively to dissipate forces away from the driver.
Kevlar panels reinforce vulnerable areas, providing additional puncture resistance. The cockpit opening features high sides and a wrap-around headrest to shield the driver’s head and neck. Roll hoops above and behind the driver offer protection in case of rollovers.
Strict regulations govern the minimum strength and dimensions of these safety features. Regular updates to chassis designs reflect ongoing efforts to maximize driver safety in Formula 1 racing.
Aerodynamics and Chassis Design
F1 car chassis and aerodynamics are intricately linked. The design of these elements directly impacts racing performance, speed, and handling on the track.
Influence of Chassis on Aerodynamics
The chassis forms the foundation for aerodynamic components. Its shape and structure affect airflow around the car. Engineers design the chassis to maximize downforce while minimizing drag.
Carbon fiber composites are used to create lightweight yet strong chassis. This allows for precise sculpting of surfaces to guide air efficiently. The chassis integrates with the floor and diffuser to generate ground effect, pulling the car to the track.
Suspension mounting points on the chassis are carefully positioned. This affects ride height and aerodynamic performance as the car moves. Chassis stiffness is crucial for maintaining consistent aerodynamics under varying loads.
Aerodynamic Elements and Body Panels
Front and rear wings are key aerodynamic elements attached to the chassis. These generate significant downforce to improve cornering grip. Wing angles can be adjusted to fine-tune performance for different tracks.
The rear wing incorporates the Drag Reduction System (DRS). This movable flap reduces air resistance on straights to boost top speed. Body panels are shaped to guide airflow smoothly over the car’s surfaces.
Sidepods channel air to cool the engine and other components. Their design balances cooling needs with aerodynamic efficiency. Bargeboards and turning vanes help direct airflow around the wheels and along the car’s sides.
The nose cone and front wing work together to manage airflow at the front of the car. Their shapes are optimized to reduce turbulence and improve overall aerodynamic performance.
Chassis Impact on Race Car Performance
The chassis plays a vital role in determining a racing car’s performance on the track. It affects weight distribution, balance, and overall handling characteristics.
Weight Distribution and Balance
A well-designed chassis optimizes weight distribution, which is critical for car balance and cornering ability. F1 cars typically have a 45/55 front-to-rear weight ratio, enhancing traction and stability. This distribution allows for better tire grip during acceleration and braking.
The chassis also influences the car’s center of gravity. A lower center of gravity improves cornering speeds and reduces body roll. F1 engineers strive to keep the mass as low as possible within the chassis design.
Aerodynamic elements integrated into the chassis further impact weight distribution. These components generate downforce, pressing the car onto the track for improved grip and stability at high speeds.
Chassis as the Backbone of Performance
The chassis serves as the foundation for all other components in racing cars, with prevalent designs such as monocoque and spaceframe. It must be rigid enough to maintain precise handling characteristics while withstanding extreme forces during cornering, acceleration, and braking.
Carbon fiber composites are widely used in F1 chassis construction due to their high strength-to-weight ratio. This material allows for a stiff yet lightweight structure, contributing to the car’s overall performance.
The chassis design also affects the placement of major components like the engine and gearbox. Proper positioning of these elements within the chassis framework can significantly impact the car’s balance and handling dynamics.
The Crucial Role of Suspensions
F1 car suspensions play a vital part in vehicle performance and handling. They connect the chassis to the wheels, managing forces and maintaining optimal tire contact with the track surface.
Chassis and Suspension Geometry
Suspension geometry in F1 cars is carefully designed to maximize grip and stability. The front suspension typically uses a push-rod system, while the rear often employs a pull-rod configuration. These setups allow for precise control of wheel movement and camber angles. The steering wheel plays a crucial role in driver control, enabling drivers to fine-tune various elements of the race car, including gear changes and adjustments to engine and braking parameters.
Engineers fine-tune suspension parameters like ride height, spring rates, and damper settings to suit different tracks and conditions. The goal is to keep tires in constant contact with the road while managing weight transfer during acceleration, braking, and cornering.
Suspension components are made from lightweight materials such as titanium and carbon fiber to reduce unsprung mass. This improves responsiveness and allows the wheels to react quickly to bumps and undulations on the track surface.
Rear Suspension Attachment and Performance
The rear suspension attachment areas are critical for managing lateral forces and power delivery. F1 cars use multi-link systems with carefully positioned mounting points on the gearbox casing and chassis.
This setup allows for independent control of camber, toe, and roll center height. Engineers can adjust these parameters to fine-tune handling characteristics and maximize traction out of corners.
The rear suspension also plays a key role in managing aerodynamic performance. Its design influences airflow around the diffuser and rear wing, affecting downforce generation. Teams constantly refine suspension geometry to balance mechanical grip with aerodynamic efficiency.
Regulations Governing F1 Chassis Specifications
F1 chassis regulations set strict rules for weight, dimensions, and design aspects. These guidelines shape the development of race cars while prioritizing safety and fair competition.
Minimum Weight and Chassis Dimensions
F1 cars must meet a minimum weight requirement of 798 kg, including the driver. This rule helps maintain a level playing field and prevents teams from gaining unfair advantages through extreme weight reduction.
Chassis dimensions are tightly controlled. The maximum width of an F1 car is limited to 2000 mm, while the maximum length is capped at 5500 mm. These restrictions influence aerodynamic designs and overall car performance.
Height regulations stipulate that no part of the bodywork can be more than 950 mm above the reference plane. This rule affects the design of wings and other aerodynamic elements.
Technical Regulations on Chassis Design
Chassis construction materials are strictly regulated. Carbon fiber composites are the primary material used due to their strength-to-weight ratio and safety properties.
Crash structures are mandatory in specific areas of the chassis. These include front, rear, and side impact structures designed to absorb energy in collisions.
The cockpit area has detailed specifications for driver safety. This includes minimum cockpit dimensions, padding requirements, and the integration of the halo device for head protection.
Fuel tank placement and construction are carefully regulated. The tank must be located between the driver and engine, utilizing specified materials for safety.
Innovations in F1 Chassis Development
F1 chassis development has seen significant advancements in design and engineering. These innovations have pushed the boundaries of performance and safety in the sport.
Evolution of Design for Competitive Advantage
Carbon fiber composites revolutionized F1 chassis construction in the 1980s. This lightweight yet strong material allowed teams to create stiffer, more aerodynamic designs. Computer-aided design and computational fluid dynamics software improved chassis optimization in the 1990s and 2000s.
Recent innovations focus on packaging components more efficiently. This includes integrating the power unit and gearbox into the chassis structure. Teams now use advanced simulation tools to test virtual prototypes before manufacturing.
3D printing has accelerated the development process. It allows rapid prototyping of complex parts and testing of new concepts. Some teams have experimented with active suspension systems to improve handling and aerodynamics.
Challenges and Triumphs in Chassis Engineering
Safety remains a top priority in F1 chassis design. The introduction of the halo device in 2018 marked a major step forward in driver protection. Engineers faced the challenge of integrating this structure without compromising aerodynamics or visibility.
Weight reduction is an ongoing battle for chassis designers. Teams constantly seek new materials and manufacturing techniques to shave off grams. This effort must balance with maintaining structural integrity and meeting safety standards.
Adapting to changing regulations presents another hurdle. The 2022 rule changes required a complete chassis redesign. Teams had to develop new solutions for ground effect aerodynamics and larger wheels. These challenges drive innovation and push the limits of engineering in Formula 1.
Impact of Chassis on Team Strategies
F1 teams adapt their chassis designs to gain competitive advantages. These strategies involve tailoring the car to specific tracks and making adjustments throughout race weekends.
Customizing Chassis to Track Specifics
Racing teams modify their chassis based on track characteristics. High-speed circuits require low-drag configurations, while tight, twisty tracks demand high downforce setups. Engineers adjust aerodynamic elements like wings and floor designs to suit each race track.
Suspension systems are tuned to handle different track surfaces. Smooth circuits allow for stiffer setups, maximizing aerodynamic performance. Bumpy tracks need softer settings to maintain tire contact and grip.
Teams balance chassis stiffness for optimal performance. Stiffer chassis improve responsiveness but can struggle on uneven surfaces. Softer designs offer better compliance but may sacrifice some precision.
Race Weekend Adjustments
F1 teams fine-tune chassis setups throughout race weekends. Practice sessions allow engineers to gather data and make informed changes. They adjust suspension components, ride heights, and aerodynamic elements to maximize performance.
Qualifying often sees teams push their chassis to the limit. They may opt for aggressive setups to secure a better starting grid position. However, these configurations might not be suitable for full race distances.
As track conditions change, teams must adapt. Temperature fluctuations, rubber buildup, and weather shifts all impact chassis behavior. Engineers work to keep the car in its optimal operating window throughout the event.
Driver feedback plays a key role in chassis adjustments. Their input helps teams refine setups, addressing issues like understeer or oversteer to improve lap times and tire management during races.
F1 Glossary: Your Comprehensive Guide To F1 Terms
Formula 1 Chassis FAQs
Do all F1 cars have the same chassis?
No, F1 teams are responsible for building their own cars, including the chassis. As the most famous motor racing sport globally, Formula One (F1) has strict rules regarding dimensions and other specifications, but teams have the freedom to design and construct their chassis within those regulations. This leads to differences in chassis design between teams, even though they may appear similar due to the convergent evolution of F1 car design.
What is the difference between monocoque and chassis in F1?
In Formula 1, the terms “monocoque” and “chassis” are often used interchangeably, as the monocoque is the main component of the chassis. The monocoque is a single-piece structure that forms the central part of the car, including the driver’s survival cell. It is made from lightweight and strong composite materials, typically carbon fiber reinforced polymer (CFRP). The monocoque provides the structural integrity and rigidity of the car, while also protecting the driver. Other components, such as the engine, suspension, and bodywork, are attached to the monocoque to complete the chassis.
How much does a F1 chassis cost?
The cost of an F1 chassis can vary depending on the team and the design, but it is estimated to be around $1,000,000 to $2,000,000. This cost includes the monocoque, which is made from expensive composite materials like carbon fiber, as well as other components such as the front and rear impact structures, suspension mounting points, and bodywork.
It’s important to note that the chassis is just one part of the overall cost of an F1 car. When you factor in the engine, gearbox, electronics, and other components, the total cost of an F1 car can range from $12 million to $15 million or more.
How many chassis are F1 teams allowed?
According to the current F1 regulations, each team is allowed to have only two cars available for use at any time during a Grand Prix weekend. This means that teams are limited to two complete chassis per event. However, teams are permitted to bring spare parts to replace damaged components, but these parts cannot be pre-assembled into a third car.
What chassis does Red Bull F1 use?
Red Bull Racing develops and manufactures its own chassis for each Formula 1 season. For the 2024 season, the team is using the Red Bull Racing RB20 chassis, which was designed and constructed in-house by Red Bull’s engineers.
Who builds Haas F1 chassis?
Haas F1 Team has a unique arrangement for the construction of their chassis. While the team is based in the United States, they have partnered with Italian manufacturer Dallara to build their chassis. Dallara is a well-known motorsports company that also supplies chassis for other racing series, such as IndyCar and Formula 2.
The design of the Haas F1 chassis is a collaborative effort between Haas and Dallara, with Haas providing the specifications and Dallara handling the manufacturing process. This arrangement allows Haas to leverage Dallara’s expertise in chassis construction while maintaining control over the design aspects of their Formula 1 car.