How Is A Formula 1 Car Made?
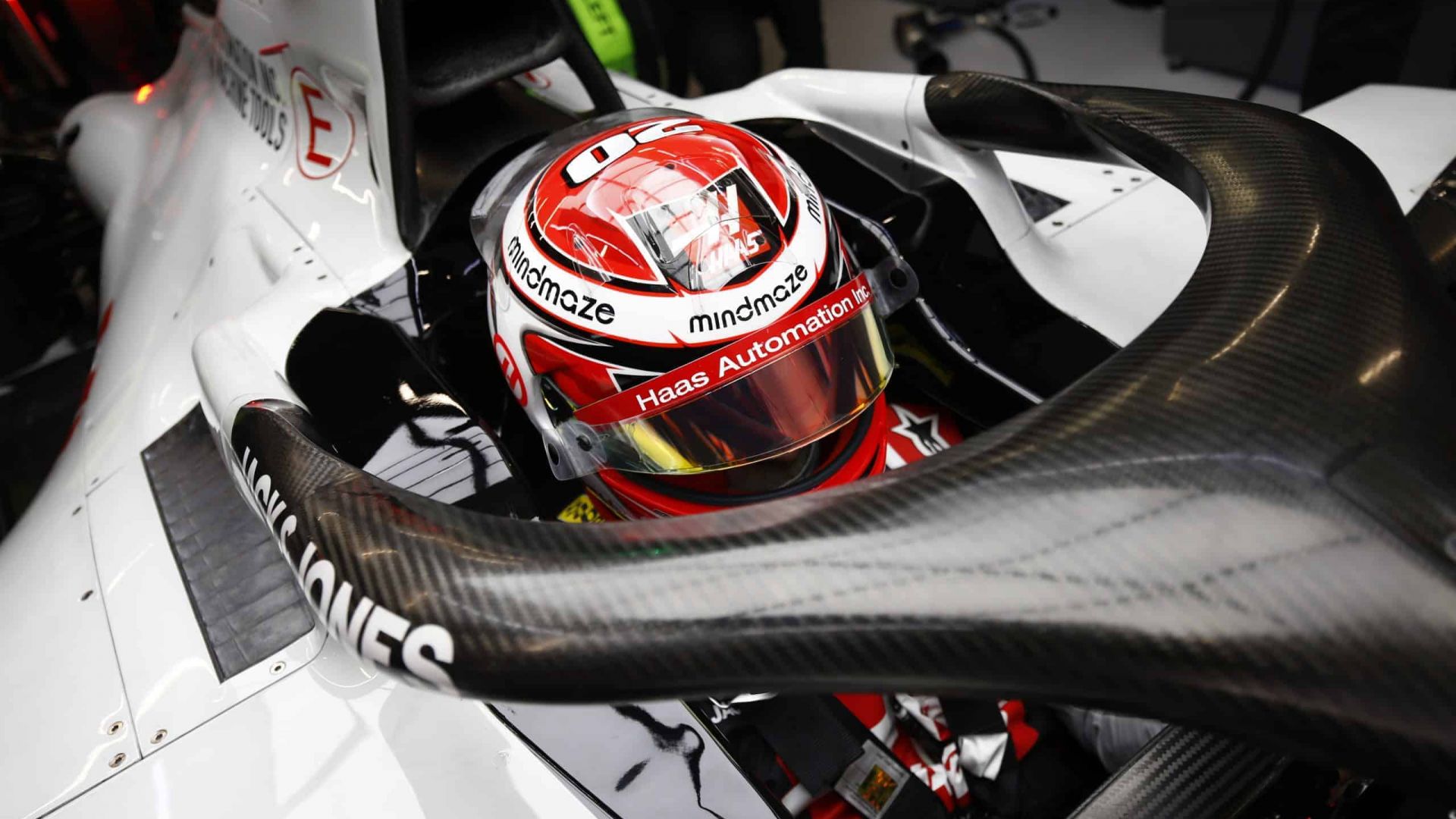
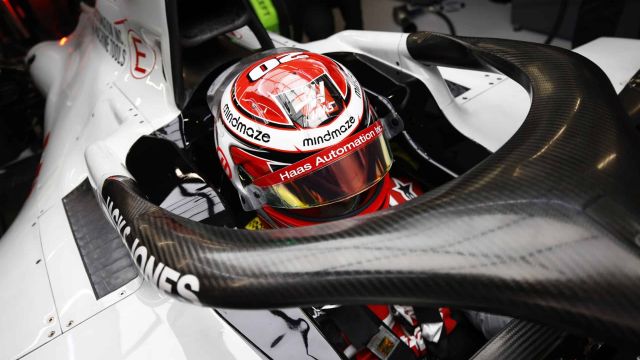
How is a FORMULA 1 car made? F1 engineers use CAD, Finite Element and Stress Analysis Software to design, analyse and refine the chassis. The following steps give a simplified view of the basic steps in the production of all carbon fibre components of the car. The main components that make up the chassis are the survival cell, roll structures, fuel tanks and ballasts.
How Is A Formula 1 Car Made?
Five-axis milling machines are employed to cut out patterns for the solid epoxy chassis. These milling machines represent the pinnacle of automotive engineering, reading data from the CAD design file to accurately replicate the dimensions and contours specified by the patterns. Should any defects be found in the patterns, they will be reproduced in the chassis derived from them, so it is critical that the patterns be defect-free.
The finished patterns are accurate to within +/- 0.05mm. Epoxy is used in place of metals to ensure that when the moulds are subjected to the extremely high temperatures of the curing process (in excess of 130 degrees) thermal expansion is reduced.
Female moulds are made from the same patterns. The production takes place in a cleanroom which is essentially a room that has been sealed off from the rest of the factory by double-door airlocks. The environment is tightly controlled (air pressure, humidity, temperature), and the workers must wear special coveralls and shoes at all times.
The moulds are constructed using carbon fibre. The process goes through several stages, being subjected to a number of vacuum treatments and layering and thermal curing processes along the way. Composite materials play a crucial role in the construction of the chassis, with regulations specifying their use to ensure safety and performance.
Upper and lower moulds are used in the production, as the chassis is built using upper and lower halves that are bonded together later. Extreme care must be exercised when removing the patterns from their moulds to avoid damaging them.
The exterior of the finished moulds are then machined to remove any imperfections. These moulds are then used to produce all the chassis needed for the season.
The chassis themselves are made from layers of carbon fibre fabric. Several different types of fabric are used in the process and the orientation of the plies is crucial – they must be aligned in a specific direction to accommodate the stiffness requirements and directional loading a particular area of the chassis will be subjected to. The use of carbon fibres is essential in enhancing the car’s performance and safety, with extensive data collection and feedback loops ensuring optimal results.
The process requires several hundred plies of carbon fabric be used for each chassis, made up of a number of different shapes, to come up with the desired properties throughout the chassis. The shapes are then cut out using computerized machines to ensure accuracy in replication from one chassis to another.
The number of plies used, and their orientation, varies from location to location around the chassis. For example, more plies are used in high-stress areas like mounting points for the suspension and the engine. The number of carbon fibre plies are counted as the layers are applied, as well as the orientation and position of each layer.
To ensure that this critical positioning of the plies is correct, workers refer to reference manuals containing annotated, visual descriptions showing exactly how each plie should be applied. Once a ply is layered, an inspector must check its position against the relevant manual and give their okay before applying the next ply.
After the plies have been laid-up in the mould in their correct position, the entire stack of plies is put into a vacuum bag and placed into an autoclave (a large oven for thermal curing under controlled temperature and pressure). The bag is then vacuumed down so that the plies are squeezed together.
The high temperatures in the autoclave interact with pre-impregnated resin in between the plies, causing it to flow evenly throughout the fabric. When the resin cures it becomes solid, fusing all of the plies together into one solid mass that represents one of the halves of the chassis. This is the time when other components can be integrated into the structure, like metal inserts and attachment studs. These will serve as mountings for various components that will be attached to the chassis later. Computational fluid dynamics is used to refine the car’s aerodynamics before the manufacturing stage. The drag reduction system, introduced in 2011, plays a crucial role in reducing drag and boosting top speed by allowing part of the rear wing to open up on straights.
The two completed chassis’ halves are then taken out of their moulds and glued together to form a single solid shell. Bulkheads are then glued to the shell to provide mountings for the front-end suspension rockers and the driver’s seatback. The areas that are to be glued together must undergo rigorous cleaning, as the sturdiness of the bond will rely solely on the glue with no support from metal fasteners. Special clamps are used when glueing the chassis halves together to ensure the process can be accurately duplicated.
A final machining and trimming process is carried out on the chassis to accommodate any required detailing and suspension pick-up points and component mounts. Again, special clamps are employed to ensure the accuracy of these processes. The energy recovery system is integrated into the chassis to maximize energy efficiency. The power unit’s cooling requirements are also considered, with main radiator inlets positioned to provide sufficient cooling.
During all the steps of the preceding process, a gruelling inspection process must be followed at every step of the way. The team will have had a Composite Inspection Department set up where all of the related parts and bonded pieces when they emerge from the autoclave and before they move on to the next stage in the assembly process, or for final introduction into the vehicle assembly. Driver safety is a top priority during these rigorous testing and inspection procedures. Reducing drag is also crucial for high-speed stability, achieved through careful design and implementation of aerodynamic features.
Parts are also brought back for inspection after every race for further inspection. Some parts are assigned an inspection/service schedule where they are automatically returned for inspection on a certain date. This may include Non-Destructive Testing (NDT) of joint bonding and laminate condition, firmness checks, visual checks, or a thorough cleaning.
Also, the chassis for any new race car must undergo a series of rigorous FIA crash tests, which they must pass before they can be approved and the car given the go-ahead for racing. These impact tests are conducted under the supervision of an FIA official. A series of tests are conducted which are divided into different groups called impact tests, roll-structure tests, and push-off tests.
It is a remarkable achievement indeed that these amazing machines are conceived, designed and built from the bottom up every year.
Video Of How A Formula 1 Car Is Made Using Carbon Fibre
This video explains how a Formula 1 car is made.
How long does it take to build a Formula 1 car?
Building a Formula 1 car is an intricate and time-consuming process that involves multiple stages, from initial design to final assembly. The entire process can span several months, with different components requiring varying amounts of time to develop and manufacture.
Design and Development
The journey begins with the design and development phase, which can take several months to complete. Engineers and designers work tirelessly to create a car that meets the latest regulations and optimizes performance. For instance, aerodynamic components, such as the front wing, can take a team of designers four to six weeks to finalize after initial wind tunnel testing.
Manufacturing
Once the design is finalized, the manufacturing process begins. This stage involves producing thousands of individual parts, each requiring precise engineering and high-quality materials. The manufacturing timeline can vary significantly depending on the complexity of the components. Some parts can be produced relatively quickly, while others, especially those made from advanced composites or requiring intricate machining, can take weeks or even months.
Assembly
After all the parts are manufactured, the assembly of the car can begin. This is a meticulous process that typically takes about a week for the initial build. During assembly, engineers ensure that every component fits perfectly and functions as intended. This stage also includes rigorous testing to verify the car’s performance and safety.
Continuous Development
It’s important to note that the development of a Formula 1 car is a continuous process. Even after the car is initially built, teams constantly work on improving and updating components throughout the racing season. This ongoing development ensures that the car remains competitive and can adapt to any changes in regulations or track conditions.
In summary, while the initial assembly of a Formula 1 car can take about a week, the entire process from design to the first race-ready vehicle spans several months. The dedication and expertise of hundreds of engineers, designers, and technicians are crucial to bringing these high-performance machines to life.
What is the Bottom of an F1 Car Made Of?
The bottom of a Formula 1 car, also known as the underfloor or plank, plays a crucial role in the car’s aerodynamics and overall performance. This component is designed to manage airflow under the car, contributing to downforce and stability.
The Plank
One of the most distinctive features of the underside of an F1 car is the wooden plank, often referred to as the skid block. This plank is typically made from a material called Jabroc, which is a high-density composite material made from beechwood veneers and resin. The plank serves several purposes:
-
Regulation Compliance: The FIA mandates the use of the plank to limit the minimum ride height of the car. This helps ensure that all teams adhere to the same aerodynamic ground clearance rules.
-
Wear Indicator: The plank also acts as a wear indicator. If the plank wears down beyond a certain limit during a race, the car is deemed to have been running too low to the ground, which can result in penalties.
Skid Blocks
In addition to the wooden plank, the underside of an F1 car is equipped with skid blocks made from titanium. These blocks are strategically placed to protect the car’s floor from damage and to create sparks when they make contact with the track surface. The sparks are a byproduct of the titanium grinding against the asphalt, which not only looks spectacular but also serves as a visual indicator of the car’s ride height.
Advanced Materials
The rest of the underfloor is typically made from advanced composite materials, such as carbon fiber. These materials are chosen for their strength, light weight, and ability to be molded into complex shapes that optimize aerodynamic performance. The use of carbon fiber allows for a rigid yet lightweight structure that can withstand the high stresses experienced during a race.
Permaglass
Some parts of the underfloor are also made from a material called Permaglass, a type of glass-reinforced plastic. This material is used for its durability and resistance to wear, further enhancing the car’s performance and longevity.
The bottom of a Formula 1 car is a sophisticated combination of materials designed to optimize performance, ensure compliance with regulations, and protect the car from wear and tear. The use of Jabroc for the plank, titanium for the skid blocks, and advanced composites like carbon fiber and Permaglass highlights the technological advancements and meticulous engineering that go into every aspect of an F1 car.
What is the Minimum Weight for an F1 Car?
The minimum weight for a Formula 1 car is a critical aspect of the sport’s regulations, designed to ensure a level playing field and to manage the performance and safety of the vehicles. As of the 2024 season, the minimum weight for an F1 car is set at 796 kilograms (1,755 pounds), which includes the driver and their full race kit (helmet, racing suit, and other necessary equipment).
Evolution of Weight Regulations
Over the years, the minimum weight limit for F1 cars has gradually increased. This change reflects the introduction of new technologies, safety measures, and hybrid power units, which have added to the overall weight of the cars. For instance, in 2022, the minimum weight was 798 kg, but it has been slightly adjusted to 796 kg for the 2024 season to accommodate various technical and regulatory updates.
Driver Weight Considerations
The regulations also stipulate a minimum driver weight of 80 kilograms (176 pounds), including the driver’s seat but excluding other equipment. If a driver weighs less than this minimum, ballast must be added to the cockpit area to make up the difference. This rule, introduced in 2019, aims to prevent teams from gaining a performance advantage by employing lighter drivers and to ensure fair competition.
Impact on Car’s Performance
The weight of an F1 car significantly impacts its performance. Heavier cars generally have slower acceleration and deceleration, affecting lap times. Therefore, teams meticulously manage the car’s weight, striving to be as close to the minimum limit as possible while ensuring structural integrity and compliance with safety regulations. The strategic placement of ballast allows teams to optimize the car’s balance and handling characteristics, further enhancing performance on the track.
Future Changes
Looking ahead, the FIA has plans to reduce the minimum weight limit for F1 cars by 40 to 50 kilograms as part of the 2026 regulations. This reduction will be facilitated by the introduction of smaller cars and wheels, aiming to improve the overall agility and efficiency of the vehicles.
In summary, the minimum weight for an F1 car in 2024 is 796 kilograms, including the driver and their race kit. This regulation ensures fair competition and safety while allowing teams to optimize performance through careful weight management and strategic ballast placement. Future changes to the weight regulations are expected to further enhance the sport’s competitiveness and technological advancement.
Some of the text for this article is from a Mercedes-AMG press release.