How Does A Formula 1 Simulator Work? Understanding Racing Sim Technology
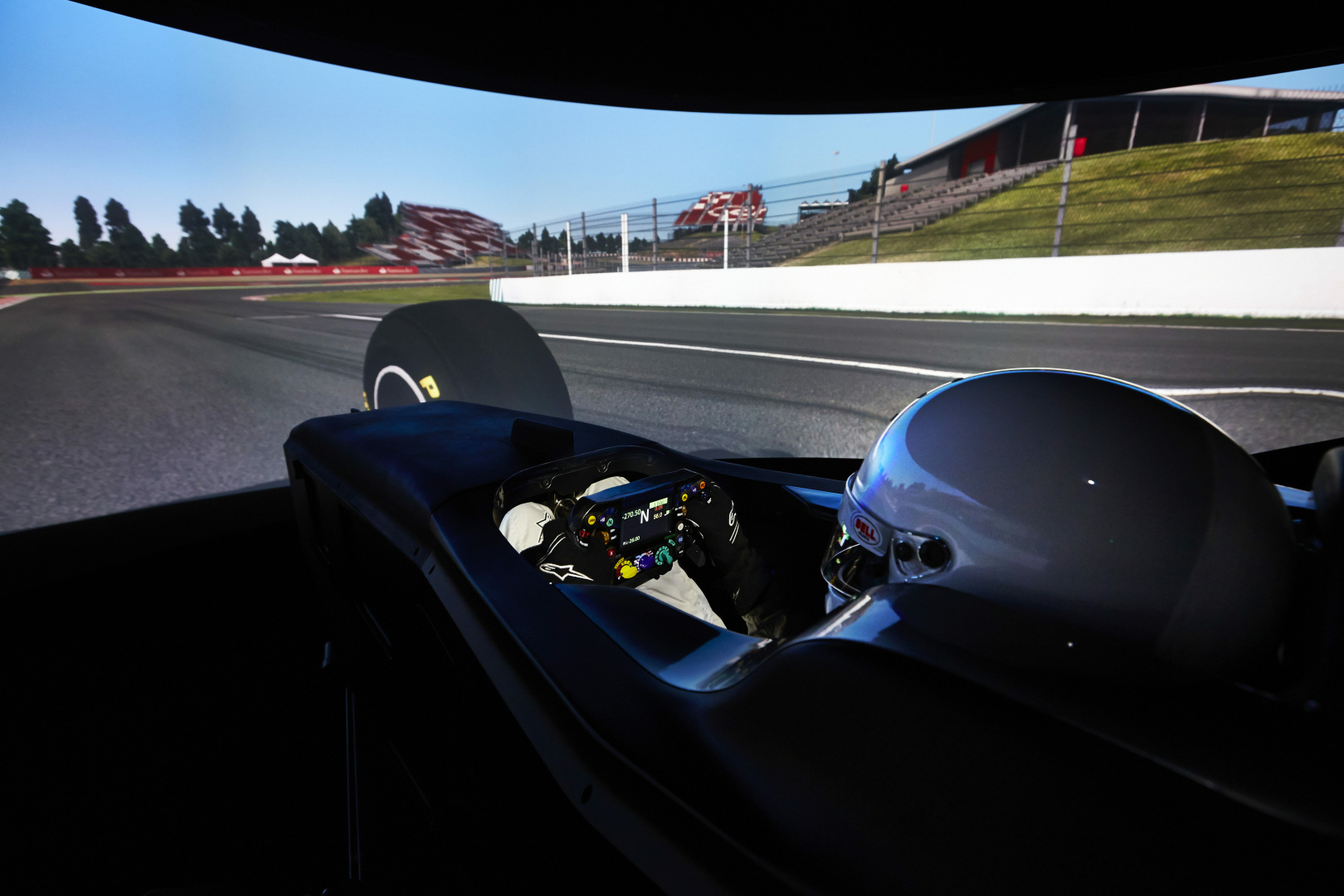
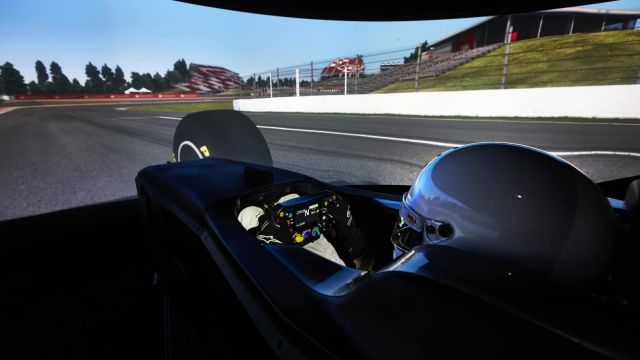
Formula 1 simulators are an integral part of a team’s development and race preparation, functioning as one of the most sophisticated tools at their disposal. These simulators provide a virtual environment where drivers can hone their skills and teams can strategize for upcoming races. In terms of construction, an F1 simulator usually consists of a model chassis, or tub, which is connected to electromechanical actuators that replicate the movements of a real car. These actuators are controlled by advanced computer systems that execute highly detailed software, simulating the experience of driving an actual F1 car on any of the tracks from the racing calendar.
The realism of these simulators is the key to their effectiveness, as they must accurately reproduce the sensations and physical challenges faced by drivers on the track. To achieve this, teams incorporate vast amounts of data—from track layouts and car performance characteristics to tire behaviors and aerodynamics—into the simulation software.
This allows drivers to experience as close as possible what they would feel in the actual car during a race weekend. Lando Norris feels this makes him a better driver come race day. “I think sim racing helps. I have improved in areas and do it whenever I need to improve. You don’t feel G-force and those things are probably the biggest things, that and the fear factor which you feel when you drive. Therefore, when I go on to the track I’m better,” said Norris. Simulators also serve as critical tools for race strategy and development, helping teams to adjust car setups and test new components before implementing them in real-world scenarios.
Key Takeaways
- High-Fidelity Training: Formula 1 simulators provide drivers with a realistic virtual environment to practice and refine their racing skills, using detailed models of tracks and cars to simulate actual driving conditions and physical challenges faced on the track.
- Strategic Development Tool: Teams utilize simulators to test and optimize car setups, experiment with race strategies, and prepare for various track conditions, making them an indispensable tool for race preparation and strategy development in the absence of extensive real-world testing time.
- Technical Sophistication with Limitations: While simulators employ advanced computational hardware, software, and lidar-scanned track data to create highly accurate racing simulations, they do have inherent limitations, particularly in replicating complex real-world variables like tire behavior under different conditions.
The Role and Purpose of F1 Simulators
Formula 1 simulators are sophisticated platforms that teams use to refine the car set-up and prepare drivers for upcoming races. They operate as virtual environments for testing race strategies, understanding circuit layouts, and optimizing performance variables.
Understanding the Simulator’s Objective
The principal aim of a Formula 1 simulator is to prepare the team for a Grand Prix event. Simulators create a precise virtual representation of real-world circuits, allowing teams to conduct extensive testing outside the limitations of physical track time. They allow for rapid iteration of car setups, mitigating potential issues before arriving at the actual racing venue.
Simulators employ detailed models of cars and tracks to help drivers and engineers identify the best configurations for suspension, aerodynamics, and other critical factors. This process is vital in gaining a competitive edge, as changes that could take significant time at the track can be tested in minutes within the simulator. Beyond setup optimization, drivers get to acclimatize to tracks, which proves invaluable, especially for new or unfamiliar circuits.
The collaborative effort of a simulator session involves not just the drivers but engineers and technical staff, all working together to translate data into actionable insights. While invaluable, the use of simulators has its boundaries; some aspects like tire behavior under varying thermal conditions and subtle track nuances are challenging to replicate precisely. Even so, their contribution is substantial in a sport where practice time is scarce and where teams constantly strive for performance improvements.
Technical Components and Setup
In the high-stakes environment of Formula 1 racing, teams leverage sophisticated simulation technology to refine car performance and driver preparedness. These systems mirror real-world conditions with impressive precision, allowing teams to conduct comprehensive analyses and preparations before hitting the actual tarmac.
Hardware and Software Infrastructure
At the core of a Formula 1 simulation are powerful computational platforms and data processing units. Teams employ cutting-edge computational hardware often provided by leading technology partners, which enables the simulation of thousands of laps within a condensed timeframe. This hardware works in conjunction with advanced software, capable of running multiple simulations in parallel, effectively multiplying the data-gathering process.
The creation of hyper-realistic track environments is facilitated by the use of lidar scanning technology, which constructs detailed 3D models of circuits. Every characteristic of the track, from the surface nuances to kerbs, is captured within these models. Teams typically collaborate on developing these models due to the rarity and high fidelity required. Together, the hardware and software create a synergy that serves as the backbone of F1 simulator technology.
- Key Hardware: High-performance computers, electromechanical actuators, data centers
- Key Software: Simulation programs (e.g., rFpro), data analysis tools
- Data Modeling: Precise 3D track mapping through laser imaging
Cockpit and Control Elements
The driver-in-loop simulator includes a chassis designed to resemble the actual F1 car’s cockpit, complete with an authentic steering wheel, pedals, and seating arrangement. This exactness extends to the control elements as well, with replicated touchpoints that provide real-time feedback akin to an actual car. For immersion, drivers often participate in simulation wearing their full racing attire.
The synchronicity between physical controls and virtual responses is critical. Actuators manipulate the cockpit in response to driver inputs, closely mimicking the car’s behavior on an actual circuit. This precise correlation supports the team in making nuanced adjustments to the car’s setup, such as changes to balance and performance similar to those made during on-track events.
- Cockpit: Replication of F1 car interior
- Control Elements: Steering wheel, pedals
- Haptic Feedback: Real-time response via electromechanical actuators
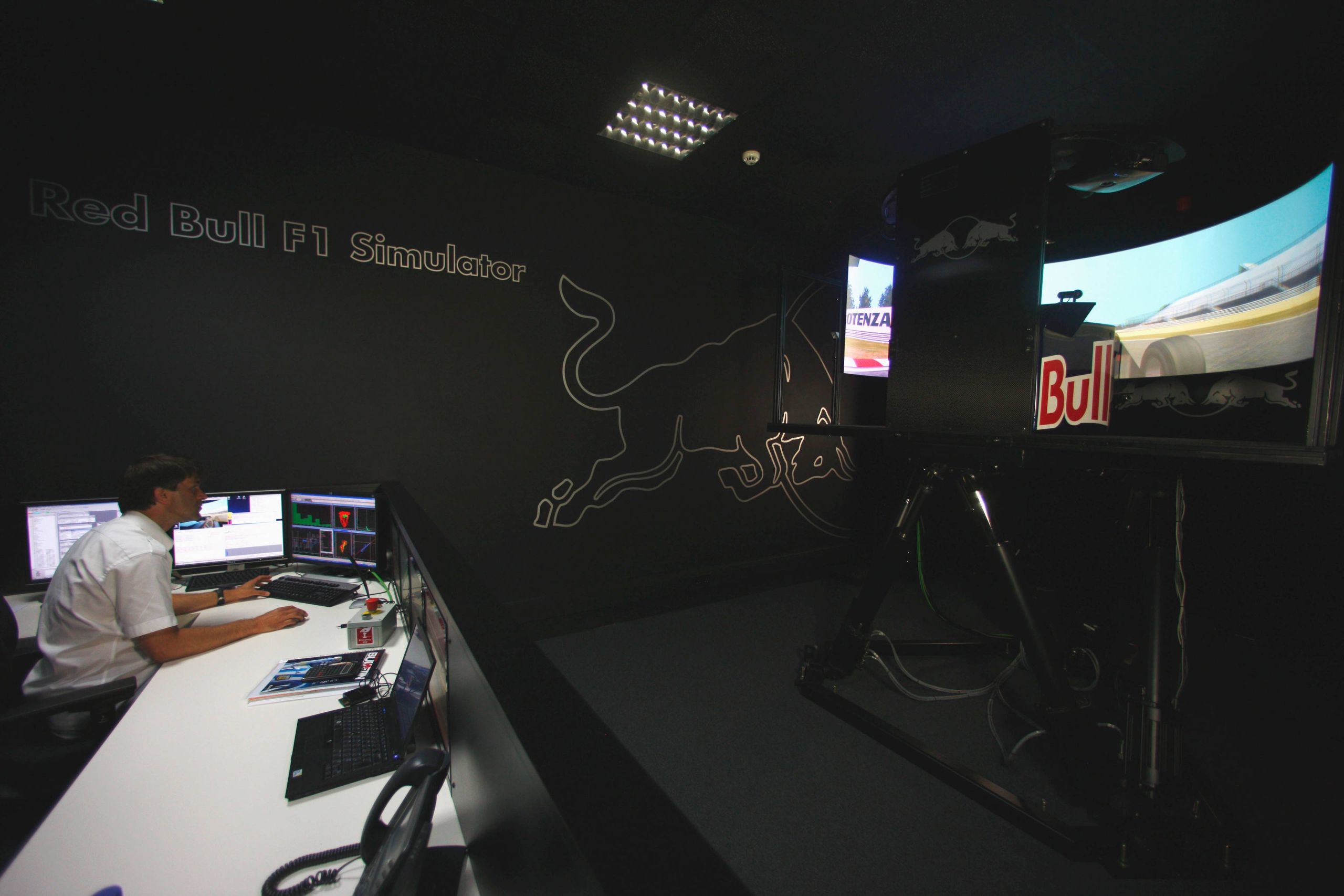
Data Integration and Simulation Accuracy
To achieve high fidelity in race preparation, Formula 1 simulators incorporate extensive track data and acknowledge their inherent limitations.
Incorporating Real-time Track Data
Formula 1 simulators integrate laser-scanned track models, which offer a comprehensive three-dimensional representation of every circuit, including surface details, kerbs, and surrounding environments. This data collection process, often conducted via lidar, ensures that each simulated track is an accurate reflection of its physical counterpart. Real-time track data, like weather conditions and grip levels, is also fed into simulations to reproduce race scenarios with higher accuracy. Teams analyze this information to refine strategies and enhance a driver’s familiarity with upcoming events.
Delineating Simulation Limitations
Despite technological advancements, fully accurate replication of a Formula 1 car’s behavior on the track cannot be achieved due to limitations in full car models and the variability in simulation effectiveness. Real-world variables, such as tire behavior under different loads and temperatures, present challenges for data integration, and as a result, cannot be perfectly emulated. This necessitates a clear understanding that while simulators are powerful tools for training and strategy development, they serve as approximations rather than exact reproductions of on-track conditions.
Interaction Between Simulators and Race Teams
Formula 1 team performance hinges greatly on the successful interaction between state-of-the-art simulators and race teams. Utilizing real-world feedback and data integration, the collaboration shapes race preparations and provides essential race weekend support.
Feedback Loops and Real-world Applications
Real-world Feedback: Teams perpetually collect data from on-track performance which feeds into the simulation models. Drivers and engineers jointly analyze this data within the simulator environment to adjust and optimize car setup and driving techniques.
- Data Integration: Teams integrate vast datasets, including telemetry and tire modeling, to simulate racing scenarios.
- Feedback Utilization: Real-time feedback from drivers about vehicle handling and performance is vital for iterative improvements.
Supporting Race Weekends and Strategy
Race Weekend Support: Simulators prove invaluable during race weekends by enabling teams to forecast vehicle behavior and strategize accordingly.
- Practice Sessions: Virtual practice sessions are used to determine optimal car settings and strategies, cutting actual track time requirements.
- Strategic Decisions: Simulators aid in deciding race strategies by allowing analysts to simulate different race conditions and outcomes.
Through this synergistic relationship, teams transform raw data into actionable insights, shaping strategies and aiding drivers in delivering peak performances.
Operational Dynamics and Access
Formula 1 simulators are advanced systems that play a pivotal role in driver training and car development. Access to these simulators is highly regulated to protect team strategies and data.
“If you utilise it correctly, the simulator can make a big difference in the development of the car. Most of our work is car development, whether for the current car or next year’s car.
“That is the testing of final components, either during or after development – that could be aerodynamic, suspension, or steering, for example. The team come up with what they believe is the right way forward, and then we test it and feedback on whether we think it is a positive or negative change,” said McLaren Test & Development driver Will Stevens.
Team and Driver Engagement
Teams frequently use simulators, providing drivers with a virtual environment to become comfortable with every circuit. The engagement covers all aspects of a race weekend, allowing teams to analyze car performance and develop strategies. Drivers have access to simulation for both learning new circuits and refining their techniques on familiar tracks.
- Team and Driver Use: Drivers and engineers collaboratively test set-ups and simulate race conditions, which are essential for continuous improvement.
- Continuous Usage: Regular use is a key component of the team’s development cycle, ensuring drivers and cars are prepared for each race.
Security, Privacy, and Use Regulation
Simulators house sensitive data that require strict control measures.
- Privacy and Exclusivity: Access to the simulator is granted under stringent rules to protect intellectual property and maintain competitive edge.
- Regulation of Use: Teams regulate simulation time to comply with sporting regulations while maintaining a balance with real-world testing.
- Team Protocols:
- Access: Limited to authorized personnel only
- Data Handling: All data encrypted and closely monitored
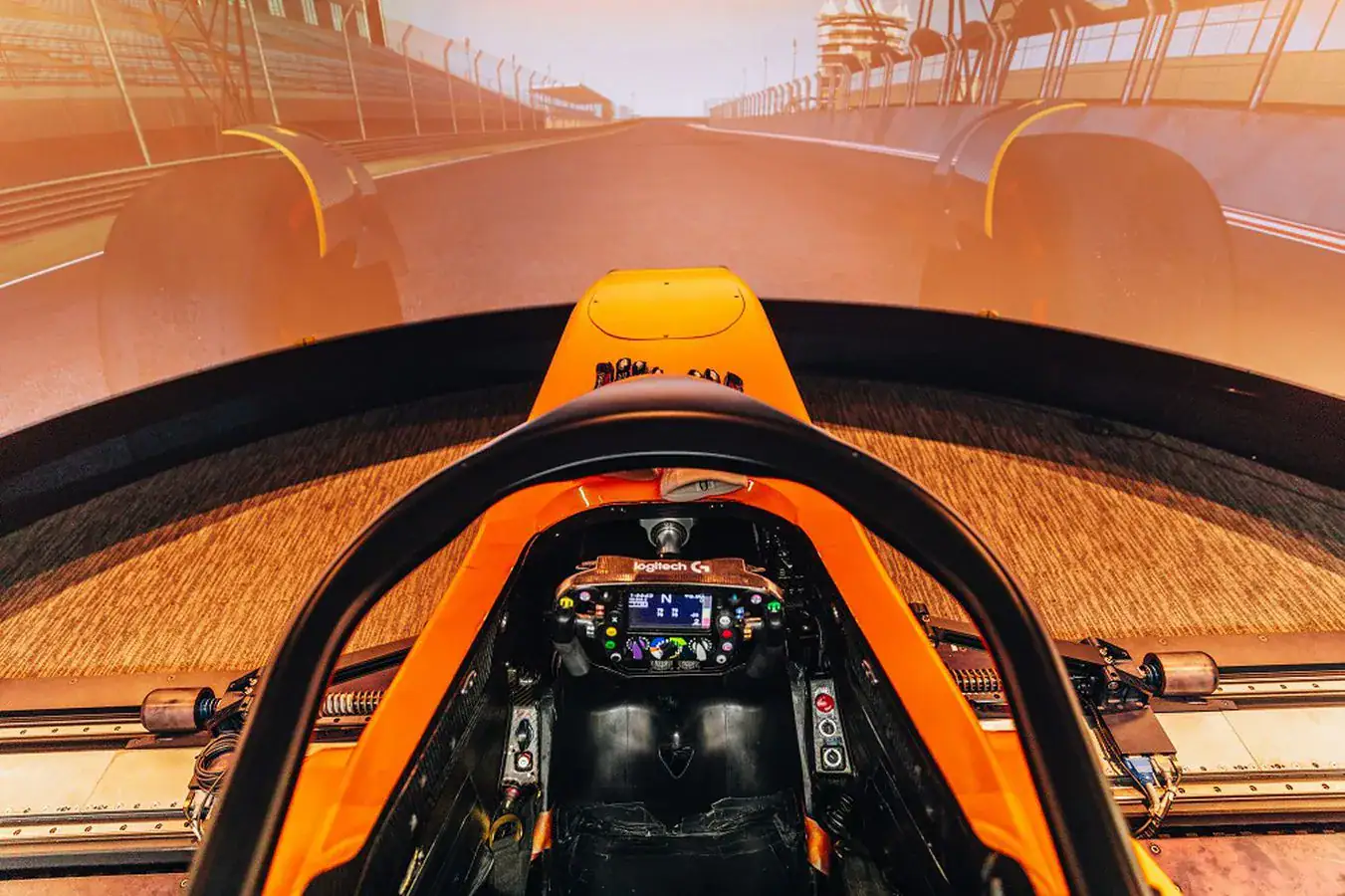
How does an F1 simulator work? FAQs
What types of simulation do F1 teams use?
There are a few areas of simulation that F1 teams use to prepare for a Grand Prix weekend, but the two main ones are driver-in-loop and computer simulation. Driver-in-loop (DiL) is effectively a virtual test track, where the car and the tracks are modelled in incredible detail, to enable us to develop the car, find the right set-up direction and help the drivers familiarise themselves with a track in a virtual environment.
Teams use a bespoke simulator facility at the factory and the DiL is somewhat similar to a professional airplane simulator used for pilot training – with the obvious difference that the “cockpit” looks like an F1 car, not a flight deck.
In a typical DiL session, race and simulator drivers can easily complete more than a full race distance. However, in that same space of time, engineers can log thousands of computer simulations as computer simulated laps can be done 100% virtually.
That means they can be sped up and run in parallel with other simulations to support both the vehicle dynamics and the strategy groups. The value of these different virtual tools is critical for an F1 team, particularly when they’ve never raced at the track before.
How accurate is the Driver in Loop simulator?
The track models used are highly detailed. They are generated by lidar scanning, where laser imaging is used to create a 3D map of the entire circuit and all of its characteristics – from track surface to kerbs and even the environment around it.
F1 teams also work with gaming companies to make the track environment as realistic as possible, as visual cues are important for the drivers to determine braking points or the right moment to start turning the car. The market for these highly complex track models is fairly small, so multiple teams will often base their simulations on the same track data and information.
The simulator itself is designed to be as realistic as possible with the same chassis, cockpit, steering wheel and pedals as the car itself, and drivers will often run in full race kit to really immerse themselves in the experience.
A significant amount of time is spent correlating the virtual model of the car to the car in the real world, so that the car can handle in the simulator just like it does out on track. This allows teams to run through set-up tweaks and changes to the car, as they would at the track, to see how it changes balance and performance.
Why is the Driver in Loop simulator so important and does the approach change for new tracks?
It’s an incredibly important part of race preparations and it’s especially vital when visiting a new track, where teams have little to no historic data. While their approach remains the same, it does mean the team is more dependent on gathering information in the simulator and as a result new circuits require a more extensive programme.
For a track that has been visited before, teams typically dedicate a two-day programme in the build-up to the event, equating to around 450 laps and roughly eight race distances, with the majority of the running completed by a team of simulator drivers.
However, when it’s a new circuit, the amount of work is much higher, with two additional days in the run-up to the event plus another day dedicated to the race drivers learning the track layout.
The bulk of the work is completed in the build-up to the race weekend, but the work doesn’t stop when the team arrives trackside. The simulator department also run a Friday programme for each Grand Prix, supporting the drivers and engineers at the track to really maximise the learnings from the first day of action.
Once the weekend is over, the sim is fired back up to conduct a post-event programme to further understand race performance and assess potential improvements.
All of this crucial pre-event work is conducted to ensure the teams arrive at the track with the car in a good enough place that the drivers can begin pushing hard from the very first laps.
How do teams use computer simulations to gather information?
Alongside the DiL programme is another virtual test track, but this time, it lives completely inside the computer itself. A racing line file is generated from the DiL to create a single trajectory around the lap and this racing line is used to complete hundreds of thousands of virtual laps ahead of each event, producing a few terabytes of data.
The engineers are able to speed up these computer simulations and run them in parallel with one another, with this much faster pace allowing a vast amount more information to be gathered in a much smaller amount of time.
From the vehicle dynamics side of things, engineers are really focused on the details – both in getting information on very specific parts, but also seeing how the car reacts to very small set-up changes. A huge number of set-up possibilities are run through the simulations and the data output – often in the form of a graph – can be compared, not only from the other runs but also overlaid on top of the DiL or real car information.
Once the data has been analysed, the teams then decide what direction to take with the car set-up for Friday’s practice sessions and this will be used as a base to start the development of the car out on track.