How Do Formula 1 Front Wings Work?
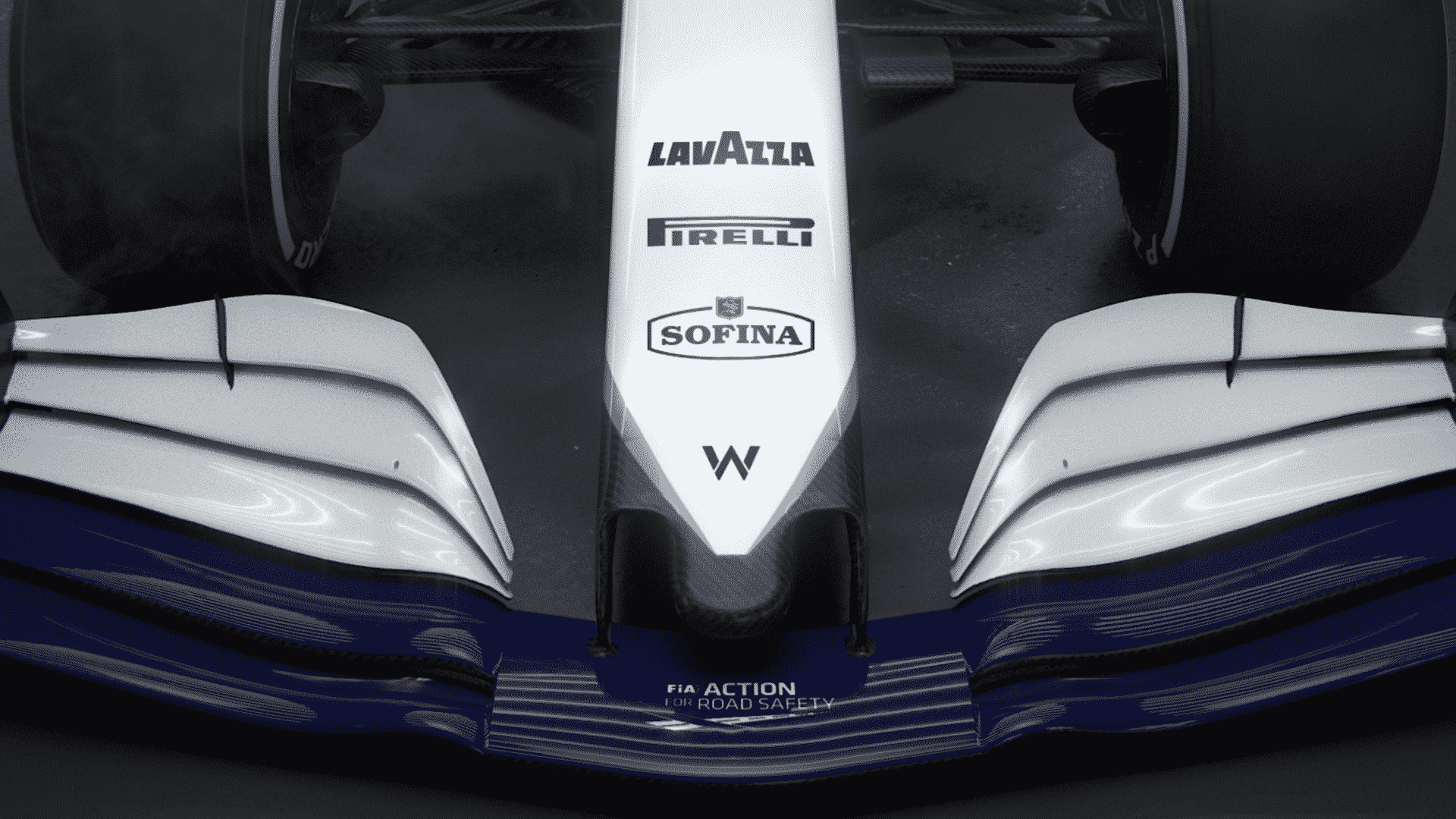
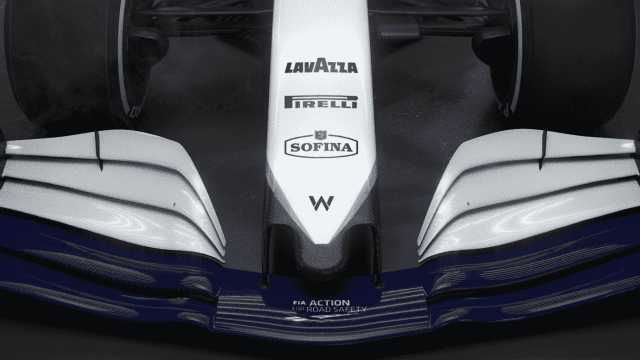
One of the most crucial components in a Formula 1 car’s performance is often overlooked: the front wing. This seemingly simple device plays a vital role in shaping the car’s aerodynamics, affecting everything from cornering speed to overall lap times. In this article, we’ll dive into the fascinating world of Formula 1 front wings and explore how they work to give drivers the edge on the track.
The front wing generates downforce and shapes airflow around the vehicle, playing a vital role in the car’s overall aerodynamic efficiency.
Front wings consist of multiple elements designed to manipulate air as it flows over, under, and around the car. These elements work together to create low-pressure areas beneath the car, increasing grip and stability. The front wing also directs air to other parts of the vehicle, such as the sidepods and floor, enhancing their effectiveness.
Engineers constantly refine front wing designs to maximize performance within the constraints of Formula 1 regulations. Small adjustments can lead to substantial gains in lap times, making the front wing a key focus of development throughout the racing season. As the first point of contact with oncoming air, the front wing sets the stage for the entire car’s aerodynamic performance.
The Role of Front Wings in Formula 1
Front wings are crucial components in Formula 1 cars, playing a vital role in aerodynamics and overall performance. These intricate structures at the front of the vehicle significantly influence airflow, downforce generation, and handling characteristics.
Downforce and Airflow Management
Front wings generate substantial downforce, pressing the car onto the track. This increased vertical force enhances grip, allowing drivers to maintain higher speeds through corners. The wings split and direct airflow around the car’s body, wheels, and underbody.
Endplates on the sides of the front wing help control airflow around the front tires. This reduces turbulence and drag, improving the car’s aerodynamic efficiency. The shape and angle of the wing elements can be adjusted to fine-tune performance for different track layouts and conditions.
Formula 1 teams invest significant resources in front wing design, constantly seeking improvements in aerodynamic performance. Even small changes can lead to meaningful gains in lap times.
Impact on Vehicle Performance
Front wings greatly affect a Formula 1 car’s balance and handling. By generating downforce at the front of the vehicle, they help counteract understeer and provide drivers with precise steering control.
The front wing’s influence extends beyond the front of the car. It sets up airflow patterns that impact the effectiveness of other aerodynamic components, such as the floor and rear wing. A well-designed front wing can improve the performance of these downstream elements.
Front wings also play a key role in brake cooling. Ducts integrated into the wing structure channel air to the brake components, helping maintain optimal operating temperatures during intense racing conditions.
Track and Speed Considerations
Front wing designs vary based on track characteristics. High-downforce configurations are used for tracks with many corners, while low-drag setups are preferred for circuits with long straightaways.
At high speeds, front wings experience significant aerodynamic loads. Engineers must balance performance with structural integrity to prevent failures during races. The wings are designed to flex slightly under load, optimizing their aerodynamic properties while staying within regulatory limits.
Track temperature and weather conditions can affect front wing performance. Teams may adjust wing settings to compensate for changes in grip levels or air density throughout a race weekend.
Design Features and Regulations
Formula 1 front wings combine complex aerodynamic elements with strict regulatory compliance. These components play a crucial role in shaping airflow around the car and generating downforce.
Endplates and Flaps
Front wing endplates serve as vertical barriers at the wing’s outer edges. They help direct airflow around the front tires and reduce turbulence. Modern endplates often feature intricate shapes and vanes to fine-tune air management.
Flaps are adjustable elements on the front wing that allow teams to modify downforce levels. These thin, angled surfaces can be adjusted between sessions to optimize performance for different track layouts. Multiple flap configurations give engineers flexibility in balancing downforce and drag.
Teams carefully design flap geometry to create pressure differentials that enhance overall wing efficiency. The interplay between endplates and flaps is critical for achieving desired aerodynamic effects.
Angle of Attack and Wing Elements
The angle of attack refers to the wing’s inclination relative to oncoming air. A steeper angle increases downforce but also creates more drag. Engineers must find the optimal balance for each circuit.
Front wings typically consist of multiple elements stacked vertically. The main plane forms the wing’s foundation, while additional elements above it help shape airflow. Gaps between elements allow air to pass through, reducing flow separation and improving efficiency.
Wing element profiles are precisely engineered to create low-pressure areas underneath the wing. This pressure differential generates downforce, pushing the car’s front end into the track for improved grip and cornering performance.
FIA Regulations and Construction
The FIA imposes strict rules on front wing design to maintain competitive balance and safety. Regulations limit overall wing dimensions, including maximum width and height. The number of wing elements and their shapes are also controlled.
Construction materials are tightly regulated. Carbon fiber composites are commonly used for their strength-to-weight ratio. Wings must pass rigorous load tests to prevent excessive flexing at high speeds, which could provide unfair aerodynamic advantages.
FIA rules also dictate minimum wing element thicknesses and maximum curvature radii. These constraints challenge designers to extract maximum performance within regulatory boundaries. Teams invest significant resources in computational fluid dynamics and wind tunnel testing to optimize their front wing designs.
Aerodynamics and Airflow Structures
Formula 1 front wings employ complex aerodynamic principles to manipulate airflow around the car. These structures generate downforce and direct air to key areas of the vehicle.
Vortices and Turbulence
Front wings create vortices that shape the airflow around the car. The Y250 vortex, formed at the junction of the front wing and nose, is particularly significant. This vortex helps manage airflow around the front tires and along the car’s sides.
Vortices also assist in reducing turbulence behind the car. By controlling air movement, front wings minimize the negative effects of dirty air on following vehicles. This aspect of aerodynamics plays a role in enabling closer racing.
Engineers design front wing elements to work together, creating a cascade of vortices. These vortices interact with each other and the car’s bodywork to optimize overall aerodynamic performance.
Ground Effect and Underfloor Aerodynamics
Front wings contribute to ground effect, a phenomenon that increases downforce as the car moves closer to the track surface. The wing’s lower elements direct airflow underneath the car, creating a low-pressure area.
This low-pressure zone effectively sucks the car toward the track, enhancing grip and cornering speeds. The front wing’s interaction with the ground is carefully balanced to maximize this effect without causing instability.
Underfloor aerodynamics work in conjunction with the front wing to further amplify ground effect. The wing channels air to the car’s floor and diffuser, boosting overall downforce generation.
Winglets
Small aerodynamic devices called winglets feature prominently on Formula 1 front wings. These structures fine-tune airflow around specific areas of the car.
Winglets can redirect air away from the front tires, reducing drag. They also help create additional vortices to manage airflow along the car’s flanks.
Some winglets assist in conditioning air before it reaches other aerodynamic components. This pre-conditioning improves the efficiency of downstream elements like bargeboards and sidepods.
Engineers must carefully design winglets to comply with strict technical regulations while maximizing their aerodynamic benefits. The precise shape and placement of these devices can have a significant impact on overall car performance.
Technological Impact and Innovations
Formula 1 front wings have undergone significant technological advancements. These components play a crucial role in aerodynamic performance, influencing the car’s overall efficiency.
Recent innovations focus on improving airflow management. Engineers design front wings to direct air around the wheels and along the car’s body. This optimization enhances downforce and reduces drag.
Cooling systems benefit from these advancements. Refined front wing designs channel air to radiators and brakes more effectively. This helps maintain optimal operating temperatures during races.
Suspension performance is also affected by front wing technology. The downforce generated impacts the car’s ride height and handling characteristics. Teams fine-tune these elements for better cornering and stability.
Slot gaps in front wings have become a key area of development. These gaps allow air to pass through the wing, improving its efficiency. Engineers carefully adjust their size and position to maximize aerodynamic benefits.
Material science contributes to front wing evolution. Carbon fiber composites offer strength and lightness. These materials allow for complex shapes that further enhance aerodynamic properties.
Computational fluid dynamics (CFD) has revolutionized front wing design. This technology enables precise simulations of airflow patterns. Teams can test and refine designs virtually before building physical prototypes.
Wind tunnel testing remains essential for validating CFD results. These facilities allow teams to fine-tune front wing designs under controlled conditions. The data collected helps optimize performance for different track layouts.
How Do Formula 1 Front Wings Work? – FAQs
Why do Formula One cars have wings?
Formula One cars have wings for two primary reasons:
1) Downforce: The front and rear wings on a Formula One car are designed to generate downforce, which is a downward force that pushes the car onto the track. This helps to increase the tire grip, allowing the car to corner at high speeds without losing traction. The increased downforce also improves the car’s stability and handling, enabling drivers to maintain control in challenging conditions.
2) Aerodynamic balance: The front and rear wings work together to maintain the car’s aerodynamic balance. The front wing is responsible for managing the airflow around the car, directing it towards the rear wing and other aerodynamic components. By carefully designing and adjusting the front wing, engineers can optimize the car’s overall aerodynamic package, minimizing drag and maximizing downforce. This balance is crucial for achieving the best possible performance on the track.
How is a Formula 1 front wing constructed?
A Formula 1 front wing is a complex aerodynamic component that is constructed using advanced materials and techniques. The typical construction process involves:
Design: The front wing is designed using computational fluid dynamics (CFD) software to optimize its shape for generating downforce and managing airflow. The design is then refined through wind tunnel testing and on-track validation.
Mold creation: Once the design is finalized, a mold is created using high-precision CNC machines. The mold is usually made from a lightweight, durable material such as carbon fiber or aluminum.
Layup: The front wing elements, such as the main plane and flaps, are constructed using a layup process. This involves placing layers of carbon fiber prepreg (pre-impregnated with resin) into the mold, ensuring the fibers are oriented correctly for optimal strength and stiffness. The outer skin is typically made of carbon fiber laminate, while the inner core consists of rohacell foam.
Curing: Once the layup is complete, the front wing elements are cured in an autoclave, which applies heat and pressure to the composite material. This process ensures that the resin is evenly distributed and that the carbon fiber layers are properly bonded together.
Assembly: After curing, the front wing elements are removed from the molds and trimmed to the required dimensions. They are then assembled, along with the endplates and other components, to form the complete front wing assembly. The endplates serve to divert the airflow outwards and around the front tires.
Finishing and testing: The assembled front wing undergoes final finishing, including painting and decal application. It is then subjected to rigorous quality control tests to ensure it meets the required specifications and performance targets.
How does a Formula 1 front wing create downforce?
In a Formula One car, only a small portion of the front wing is used to create downforce. The rest of the wing regulates the airstreams around the portions of the car in their wake. The endplates and the inner arched portion of the front wing flaps contribute to the generation of downforce.
The lateral pressure created by the gradients in the front wing creates vortices that contribute towards the downforce in the car. After all, the front wing contributes up to 40 per cent of the downforce generated in a car. The front wing, being close to the track, also contributes to creating the maximum ground effect and increasing the generated downforce.
Before 2009, the cars had continuous aerofoil sections from one end of the wing to another. Before then, cars had only two or three aerofoil sections. These sections created enough downforce for the cars to get a firm grip on the track. But in 2009, the FIA came out with a regulation that required a clear section of 250mm on either side of the centre of the nose. This forced the aerodynamicists to increase the number of aerofoils on the wing.
How do front wings improve the aerodynamics of a Formula 1 car?
The downforce generated by the front wings comes at a price. This generation of downforce has a penalty of increasing the drag on the car. Any drag is detrimental to the performance of the car. The front wing has to be so designed that they compensate for the drag created by them. This is where the streamlining of airflow around the car comes in.
Until 1998, the endplates were just that; endplates. The vortex of air that creates the downforce also interferes with air rotating around the front wheels. This turbulent air affects the performance of the big wheels and hence that of the car. Endplates were therefore modified to direct the airflow between the wheels rather than at them.
If the front wing leaves a turbulent wake, different parts of the car will be affected by the turbulence creating a drag. This will affect the performance of the car. It is for this reason that the different mini flaps reduce in height closer to the nose. It is this asymmetry that enables the wing to regulate the airflow in its wake.
The shape of the mini wing enables it to direct the stream not used for creating downforce towards the side pods. It is this stream that cools the air-cooled engine of the car. Without the help of the slipstream the engine would heat up and the car would stall. The engine radiator uses this air to cool the engine and improve the performance of the car.
How much does the front wing of a Formula One car cost?
The front wing is the most important component that determines the aerodynamic streamlining of a Formula One car. This makes it one of the last components designed for a new car. The shape and the bodywork of the car will determine the construction of a wing. As a result, the front wing goes through a lot of aerodynamic trials before it is finalised.
The aerodynamic trials, simulated and on-track, are what make the front wings of a Formula One car costly. The cost of the materials used in constructing the front wing pale in comparison to the simulations and trials involved in a car wing. Both the constructor of the car and the driver will understandably want to get the maximum out of the wing.
The cost of a good front wing could easily go upwards of USD 300,000. Much depends on the budget of the team and its aspirations. Many teams go for lower-cost front wings. But front wings are studied constantly and modified as required to obtain optimal aerodynamic performance.