How Do F1 Teams Deliver Upgrades?
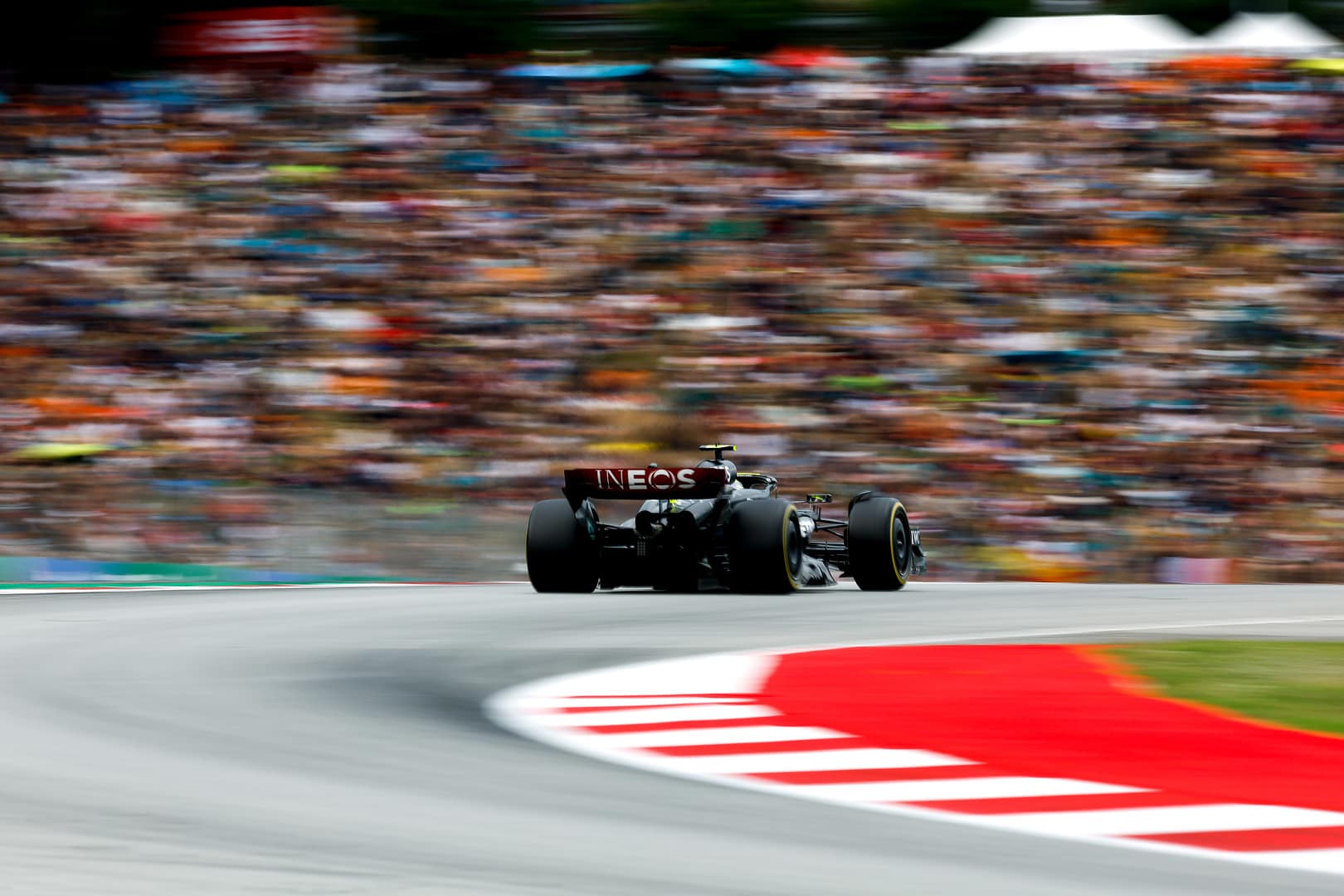
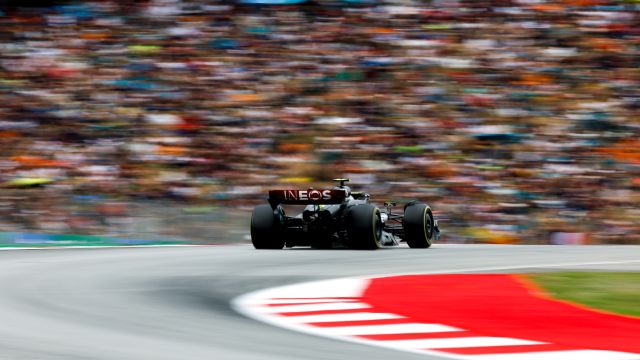
Formula One racing is all about finding the right balance between learning about newer grades and maximizing the performance of a specific race weekend. Developing a Formula One car involves two parts: aerodynamic development and chassis development. The former includes the weighted surfaces of the car visible from the exterior, while the latter includes underlying parts such as suspension, steering, and brakes. In addition to the underlying development rate of the car, there are also event-specific developments that the team targets, such as a low downforce rear wing for events like Spa.
Developing the Formula One Car
Aerodynamic Development
One of the key aspects of developing a Formula One car is aerodynamic development. This involves improving the weighted surfaces of the car that are visible from the exterior. The process starts by identifying areas where the airflow around the car can be improved. The team then comes up with different ways to target these areas within the regulations. They run simulations to understand if they can manipulate the flow field as desired. If successful, they take it into a wind tunnel test to understand if it improves the aerodynamic performance.
Chassis Development
The second part of developing a Formula One car is chassis development. This involves improving the underlying parts of the car such as suspension, steering, and brakes. The team spends a lot of time developing these components to ensure they perform as expected. The manufacturing process involves multiple departments, starting from the release of the surface by the Aero group to the design, pattern, mold, and composite lamination. There are also tests involved to ensure structural integrity.
Event-Specific Developments
In addition to the underlying development rate of the car, there are also event-specific developments that the team targets. For example, they may use a low downforce rear wing for events such as Spa. The development direction can also change depending on the feedback received from the car’s behavior on track. The team may change the areas they want to improve or steer what they might do next. The data they collect is very specific to the question they are trying to answer, such as whether a new lightweight part will be strong enough or whether an upgrade will make the car faster. The driver feedback is also pivotal in knowing if a new upgrade performs as intended.
Aerodynamic Upgrade Process
Identifying Areas for Improvement
The first step in the aerodynamic upgrade process is identifying areas for improvement. This involves analyzing the airflow around the car and determining what can be done to manipulate it in a way that will improve the car’s performance. This process is done in collaboration with the Aero group and involves a mixture of testing, simulations, and wind tunnel tests.
The goal is to identify what needs to be improved in terms of the car’s aerodynamic performance and then come up with different ways to target those areas within the regulations that are in place. The areas that are targeted may be specific to the event, such as a low downforce rear wing for events like Spa, or may be a general aerodynamic upgrade.
Testing and Optimization
Once an area for improvement has been identified, the next step is testing and optimization. This involves running simulations to determine if the desired flow field can be manipulated in the desired way. If the simulation is successful, the upgrade is taken into a wind tunnel test to determine if it has improved the car’s aerodynamic performance.
The data that is collected during testing is very specific to the particular question that is being answered. For example, if the question is whether a new lightweight part will be strong enough, then the stresses and forces on the part are the most important things to consider. If the question is whether an upgrade will make the car faster, then the lap time improvement and how it comes about are the most important things to consider.
Once an upgrade makes it to the track, it is analyzed in three main areas. First, the performance improvement is compared to the previous component. Second, any characteristic changes are noted, such as improvements in particular corners or phases of the corners around the circuit. Finally, the results are compared to the expected results from the wind tunnel. This data is used to determine which corners around the circuit the performance improvement will be the largest.
In conclusion, the aerodynamic upgrade process is a complex and collaborative effort that involves identifying areas for improvement and testing and optimizing upgrades. The goal is to improve the car’s aerodynamic performance and maximize its performance on race weekends. The process involves a great deal of testing and data analysis, and the feedback from the drivers is pivotal in determining whether upgrades are performing as intended.
Data Analysis and Simulation
Component-Level Analysis
The process of developing a Formula One car involves constant evolution and improvement. One of the key aspects of this process is component-level analysis. The team works to ensure that every component of the car is strong enough and light enough to perform as expected. This involves a lot of testing and development work, both in simulation and in real-world scenarios.
To determine whether a new lightweight part will be strong enough, the team focuses on stresses and forces. If they are trying to determine whether an upgrade will make the car faster, lap time improvement and how that lap time comes is also important. The team gets a vast array of data, but it is very specific to the particular question they are trying to answer. Once they have the data, the job of the team is to look at all those squiggly lines and find that lap time.
Driver-in-the-Loop Simulator
The driver-in-the-loop simulator is a hybrid between the real world and the simulation world. It’s a place where the team’s race drivers can jump in and experience a virtual version of the car before it ever becomes a reality. This simulator is a valuable tool for the team, as it allows them to test and refine the car in a safe and controlled environment.
The simulator is also used to gather feedback from the drivers. They are able to pinpoint specific events around the lap and provide feedback to the engineers. This feedback is crucial in helping the team understand if a new upgrade is performing as intended.
Simulation Tools
In a cost-cut world, more so than ever, it is vital that the team uses simulation tools to determine whether their upgrades will deliver on-track performance. The team puts a great emphasis on planning for a new car or performance updates. They start planning these upgrades well in advance of the actual build or delivery window.
The team uses a variety of simulation tools to test and refine the car. They start at a component level and work their way up to lap simulations. This allows them to understand how to make the car go faster and identify areas that need improvement. They also use wind tunnel data to feed into their simulation tools, which allows them to see which corners around the circuit will see the largest performance improvement.
Once an update makes it to the track, the team analyzes it by comparing it to the previous component, checking for any characteristic changes, and comparing the results back to the expected results from the wind tunnel. The team also relies on driver feedback to determine if the upgrade is performing as intended.
Manufacturing Process
Team Effort
The manufacturing of aerodynamic composite components is a big team effort at the factory. There are many different departments involved, from aerodynamics to design, to manufacturing. The process starts with the aerodynamics department releasing the surface, which is then reduced to a model or drawing by the design department. The manufacturing department then produces a pattern, followed by a mold, and finally, the composite component is laminated. Afterward, pre-fit work is done to ensure quality control. There are also test and development steps involved, including non-destructive testing for structural integrity.
Planning and Reactivity
Planning is crucial in the manufacturing process, as it takes a lot of time and effort to develop a new car or performance upgrade. The team starts planning a new car a year in advance of the actual build window or shakedown. For performance updates, the team plans a couple of months ahead of the delivery date.
However, the team is also very reactive and can respond quickly to any damage incurred during a race weekend or if a performance item needs to be brought forward. For smaller components, they are easier to fit at the circuit, and the team can analyze the aerodynamic data in real-time. For larger aerodynamic upgrades, it’s a bit more difficult to fit them into a single race weekend, so the team has to ensure they collect enough data from previous races to compare and analyze the upgrade’s desired effect on performance.
When analyzing an upgrade’s performance, the team compares it to the previous component, checks if they are getting the intended performance improvement from the aerodynamic sensors on the car, and looks for any characteristic changes, such as improved performance in particular corners or phases of the corners around the circuit. Finally, they compare the results to the expected results from the wind tunnel, which also feeds into their simulation tools, allowing them to see which corners around the circuit they think the performance improvement will be at the largest.
In conclusion, manufacturing aerodynamic composite components is a team effort that involves many different departments. Planning is essential, but the team must also be reactive to any changes that may occur. Analyzing an upgrade’s performance involves comparing it to the previous component, checking for performance improvements, and comparing the results to the expected results from the wind tunnel.
On-Track Analysis
When a new upgrade is brought to the track, the team needs to analyze its performance to ensure it is having the desired effect. This analysis is split into two main areas: comparing results and driver feedback.
Comparing Results
To compare the results of the new upgrade, the team looks at three main areas. Firstly, they compare the performance of the new component to the previous one to ensure they are getting the expected performance improvement. Secondly, they look for any characteristic changes, such as improvements in specific corners or phases of the circuit. Finally, they compare the results back to the expected results from the wind tunnel.
This wind tunnel data also feeds into the team’s simulation tools, allowing them to see which corners around the circuit they think the performance improvement will be the largest. This information is crucial for the team to optimize the car’s setup towards qualifying and the race.
Driver Feedback
Driver feedback is pivotal when bringing a new upgrade to the track. The drivers are excellent at pinpointing specific events around the lap and relaying this information to the engineers. After the debrief, the team can gather and analyze these specific examples to determine if the upgrade is performing as intended.
The team needs to know exactly what the expectations are in terms of car balance and see if they can match those expectations. If the expectations are translated into the behavior on track, it is a good sign that the upgrade is performing well.
In conclusion, the team’s on-track analysis is a crucial part of the development process. By comparing results and gathering driver feedback, the team can optimize the car’s performance and ensure that upgrades are having the desired effect.
Watch: How Do F1 Teams Design, Produce and Race an Upgrade?
Mercedes-AMG Petronas explain how they design, produce, and race an upgrade to their car.